Borosilicate Glass for Anondic Bonding
A postdoc requested the following:
We are looking for 500 um thick, 100 mm diameter borosilicate glass double-side polished wafers for anodic bonding. I was examining your online inventory and saw some borofloat-33 wafers (ID# 517) that appear to be the right dimensions. However, I do not know if these wafers will serve for anodic bonding, since I don't see TTV, surface roughness, bow, or warp listed. Additionally, it would be helpful to know the thickness tolerance of the wafers (if known).
Additionally, if you have any alternate suggestions as far as 500 um thick 100mm diameter borosilicate wafers you have in inventory, I'd be happy to hear them.
Reference #188151 for specs and pricing.
Anondic Bonding Glass & Silicon
We have a large selection of glass and silicon with tight Total Thickness Variation (TTV) across the wafers. These ultra-flat surfaces allow extremely tight seals for all your needs. Please contact us today for an immediate quote!
Get Your Quote FAST!
Video: Learn About Anondic Bonding
Thermal Oxide Coated Silicon Wafers to Fabricate Microfluidic Channels
An assistant research scientist requested a quote for the followng.
I need your recommendation on selecting the right oxide wafer. I am currently etching Si to fabricate microfluidic channel. After etching I will work through glass bonding (anodic bonding) to the top side of Si wafer.
I would like to get for: deposit both side thermal oxide on a 4 and 6 inch silicon wafer with one micrometer oxide layer.
To select the right oxide wafer for fabricating microfluidic channels and performing anodic bonding, several factors must be considered, including the type of silicon wafer, the thickness of the silicon dioxide layer, and the specific requirements of your application. Here are some recommendations:
-
Silicon Wafer Specifications:
- Type: Typically, you would use a <100> or <111> silicon wafer. The <100> Ori is more common for microfluidics due to its easier anisotropic etching properties.
- Doping: For anodic bonding, using a high-resistivity, lightly doped (n-type or p-type) silicon wafer is recommended.
- Thickness: Choose a wafer thickness that provides mechanical stability during processing. Common thicknesses range from 400 µm to 600 µm.
- Silicon Dioxide (SiO2) Layer:
- Thickness: The oxide layer thickness depends on your specific etching requirements and the depth of the microfluidic channels. A common range is between 500 nm and 2 µm.
- Uniformity: Ensure the oxide layer has a uniform thickness across the wafer to achieve consistent etching and bonding results.
- Oxide Type:
- Thermal Oxide: This type provides a high-quality, dense oxide layer and is ideal for applications requiring excellent dielectric properties and strong adhesion.
- PECVD Oxide: If lower temperatures are required for your process, Plasma-Enhanced Chemical Vapor Deposition (PECVD) oxide might be suitable. However, it generally has lower density and may not be as robust as thermal oxide.
- Considerations for Anodic Bonding:
- Ensure the silicon wafer is clean and free of contaminants that could interfere with the bonding process.
- The silicon dioxide layer can act as an electrical insulator during anodic bonding, so it’s essential to have a proper alignment and ensure good contact between the silicon and the glass.
- Use a Pyrex or Borofloat glass wafer, which has similar thermal expansion properties to silicon, to prevent stress and cracking during bonding.
Summary Recommendation:
- Silicon Wafer: <100> Ori, high-resistivity, lightly doped, 400-600 µm thick.
- Oxide Layer: Thermal oxide, 500 nm to 2 µm thick, uniform and high quality.
- Glass Wafer: Pyrex or Borofloat, compatible with anodic bonding.
Ensure your processing steps, including etching and cleaning, are optimized for the specific wafer and oxide layer you choose.
Reference #312732 for specs and pricing.
What Substrates Can Be Used for Anondic Bonding?
Anodic bonding is a process used to bond a glass substrate to a silicon or another glass substrate. The process uses an electric field to bond the substrates at the atomic level. The choice of substrate materials for anodic bonding depends on the specific application and the requirements of the bonded structure.
The following are some examples of substrates that can be used for anodic bonding:
-
Silicon to glass: This is a common substrate combination used in microelectronics and MEMS applications.
-
Glass to glass: This is used in the production of various optical devices, such as microfluidic devices, and for packaging of microelectronic components.
-
Silicon to silicon: This is used in the production of silicon-based sensors, such as pressure sensors, acceleration sensors, and gyroscopes.
-
Glass to metal: This combination is used in the production of various sensors and microelectronic devices.
-
Glass to ceramics: This combination is used in the production of sensors, fuel cells, and other high-temperature applications.
In general, any combination of materials that can withstand the anodic bonding process can be used for anodic bonding. However, the coefficient of thermal expansion (CTE) of the materials should be similar to prevent cracking or delamination of the bonded structure due to thermal mismatch during subsequent processing.
How Does Anondic Bonding Work?
Anodic bonding is a process by which glass is sealed to metal without using an intermediate layer. This method is commonly used to seal glass to silicon wafers, which are used in electronics and microfluidics. It is also a popular technique for microfluidics. Anondic bonding is a highly effective means to seal different materials. In fact, it is one of the only methods that can seal metal and glass together.
Investigating Different Ways to Clean Wafer Surfaces for the Anondic Bonding Process
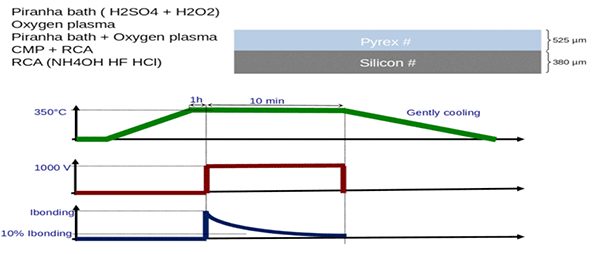
In order to create an anodic bond, two substrates must be heated to the same temperature. In addition, the glass must be made of a material that readily forms an oxide film. The glass must have a high concentration of sodium, such as Borofloat 33 (BF33). The high-temperature-and-pressure environment required in the anodic bonding process is ideal for a silicon-glass interface. The process requires a high amount of electrical current to work properly.
The glass layers are then placed on the silicon wafer. The silicon layer is then pressed against the glass, creating an anodic bond between the two. The glass layer can be applied with a needle or a full area cathode electrode. Once the surface of the glass is sufficiently prepared, the sodium ions are then displaced from the surface of the silicon. This process is called anodic bonding.
In contrast to electroplating, anodic bonding can also be used for vacuum packaging of microelectronic devices. While anodic bonding involves applying a high voltage, it is not as efficient as electroplating. In contrast to a conventional welding process, anodic bonding can be achieved with a relatively low temperature. The process is faster than that of anodic bonding. It also does not require an intermediate layer.
Anodic bonding is a process that involves applying a high voltage across the glass. The glass must be free of particles to ensure a permanent bond. The process is used in electronic applications. Anodic bonding is a great option for wafer level packaging. The technique allows for the safe handling of small electronic components. There are no adhesives and high-voltage fields. The process can be done quickly and safely.
While anondic bonding is not compatible with microelectronic devices, the high voltages used for the process makes it less convenient. The high voltage can result in a low-voltage-only semiconductor. As a result, anodic bonding is a better option compared to direct bonding. The process is more reliable. Anodic bonding with anodic parts. Consequently, anodic bonding is an excellent choice for packaging.
Anodic bonding is another method of joining glass to silicon. The process requires no intermediate layer. It is a permanent bond between the glass and the silicon. This process is known as electrostatic sealing. It is commonly used to seal glass to silicon and other surfaces. Although anodic bonding is not completely compatible with semiconductors, it can be used to seal metals. The latter is an advantage of anodic bonding because it is easy to do.
Anondic bonding is a relatively simple procedure that can yield results of high-quality silicon wafers. It involves bonding two metals with one another. Anondic bonding is an ideal solution for applications that require high-quality silicon. If you have a low-quality component that requires high-quality glass, anondic bonding is a good option. The bonding process can be carried out at room temperature or at high temperatures.
The advantages of anondic bonding are two-fold. The first is that the process requires a low-temperature environment. The second is that the process uses low-temperature alloys. Both types of anondic bonding are hermetic. While eutectic bonding has the highest temperature, eutectic bonding is the best option for high-volume production. You can use a vacuum to ensure the process is as clean as possible.