Bonding SOI to Glass
A PhD candidate requested a quote for the following:
I'm looking for a service for anodic bonding. We would need to bond 200mm SOI-wafers with cavities to 200mm Borofloat33 wafers. Annual volume is few tens of wafers.rnrnWould you give feedback that do you have a service available to discuss further in more detail.
We quote using atomic diffusion bonding, not anondic bonding.
Reference #302417 for specs and pricing.
Get Your Quote FAST! Or, Buy Online and Start Researching Today!
What are The Advantages and Disadvantages Between Atomic Diffusion Bonding and Anondic Bonding?
Atomic diffusion bonding and anodic bonding are both precision joining techniques used to create strong, reliable bonds between materials, often employed in the semiconductor and microelectronics industries. However, they differ significantly in their mechanisms, applications, and the types of materials they can bond. Here’s a detailed comparison:
Atomic Diffusion Bonding
Mechanism:
- Process: Atomic diffusion bonding relies on the diffusion of atoms across the interface of the materials being joined. This occurs under high temperature and pressure, but below the melting point of the materials.
- Conditions: The materials are brought into intimate contact, and temperature and pressure are applied for an extended period to allow atoms to migrate and form a strong bond.
Materials:
- Typically used for metals and ceramics.
- Can bond similar and dissimilar materials, provided they can withstand the high temperatures and pressures involved.
Applications:
- Aerospace components, such as jet engine parts.
- Microelectronics and MEMS (Micro-Electro-Mechanical Systems).
- Medical devices requiring high-strength, biocompatible joints.
Advantages:
- Produces high-strength, high-integrity bonds.
- Minimal deformation due to the solid-state nature of the process.
- Suitable for high-precision applications.
Challenges:
- Requires precise control of temperature and pressure.
- Surfaces must be extremely clean and smooth to achieve effective bonding.
Anodic Bonding
Mechanism:
- Process: Anodic bonding involves the application of an electric field between the materials to be bonded, typically a glass substrate and a conductive material (often silicon). This process creates a strong electrostatic attraction that bonds the materials.
- Conditions: The glass is heated to a temperature where it becomes ionically conductive (usually between 300°C and 500°C). An electric field (typically several hundred volts) is then applied across the interface.
Materials:
- Primarily used to bond silicon to glass.
- Can also bond other conductive materials to glass or other ionically conductive materials.
Applications:
- Microelectromechanical systems (MEMS), such as sensors and actuators.
- Encapsulation of electronic components.
- Fabrication of microfluidic devices.
Advantages:
- Can create hermetic seals, which are crucial for certain microelectronics and MEMS applications.
- Lower temperatures compared to some other bonding techniques, reducing thermal stress.
- Allows bonding of materials with significantly different thermal expansion coefficients.
Challenges:
- Limited to materials that can withstand the required temperatures and electric fields.
- Requires precise alignment of the materials to ensure a uniform bond.
Summary
Atomic Diffusion Bonding:
- Mechanism: Atom migration under heat and pressure.
- Materials: Metals and ceramics, similar and dissimilar.
- Applications: Aerospace, microelectronics, medical devices.
- Advantages: High-strength, precision bonds.
- Challenges: High temperature and pressure, surface preparation critical.
Anodic Bonding:
- Mechanism: Electrostatic attraction with an electric field.
- Materials: Conductive materials (e.g., silicon) to glass.
- Applications: MEMS, microelectronics, microfluidics.
- Advantages: Hermetic seals, lower temperature, bonding of different materials.
- Challenges: Requires ionically conductive material, precise alignment.
Both techniques are essential in advanced manufacturing and microfabrication, each suited to specific material combinations and application requirements.
What is Diffusion Bonding?
When it comes to fusing semiconductor materials for top-notch applications—think the brains behind your gadgets or microscopic machines—diffusion bonding is the go-to method. It guarantees bonds that are not only precise but also incredibly strong. Here’s how diffusion bonding is applied and its significance in the semiconductor industry:
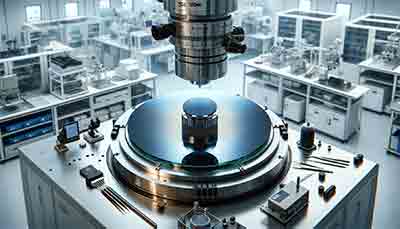
Process in the Semiconductor Industry
- Surface Preparation : Semiconductor wafers or components are cleaned and polished to create ultra-smooth surfaces. Making sure everything touches down at the atomic level is key here.
- Alignment and Clamping : The components to be bonded are precisely aligned and clamped together under pressure to maintain contact throughout the bonding process.
- Heating : The assembly is heated to a specific temperature, typically in a vacuum or controlled atmosphere to prevent oxidation and contamination.
- Holding : The temperature and pressure are maintained for a specified duration to allow atomic diffusion across the interface, forming a strong bond.
Key Applications
-
Wafer Bonding : Diffusion bonding is used to bond semiconductor wafers made of silicon, silicon carbide, gallium arsenide, and other materials. When it comes to building the complex insides of cutting-edge tech like microprocessors or tiny machines, getting those layers perfect is key.
-
MEMS Fabrication : In MEMS, diffusion bonding is used to create complex microstructures by bonding silicon wafers or other substrates. Dive into making small-scale devices like sensors and actuators? Then getting this procedure right is your ticket in.
-
3D Integration : As devices become more compact and powerful, there is a growing need for three-dimensional (3D) integration of semiconductor devices. With diffusion bonding, it’s like playing Tetris with technology; you stack those pieces—the active devices—neatly for higher efficiency without taking up much room.
-
Optoelectronics : Diffusion bonding is employed in the fabrication of optoelectronic devices, such as LEDs and photonic circuits, where precise alignment and strong bonds are critical for device performance.
Advantages in the Semiconductor Industry
- High Precision : Diffusion bonding allows for atomic-level alignment and bonding, which is essential for semiconductor applications where precision is paramount.
- High Strength and Integrity : The bonds formed through diffusion bonding are typically as strong as the parent materials, ensuring the reliability and durability of semiconductor devices.
- Imagine being able to merge unlike materials into one durable union; that's what we excel at. : Think of it as matchmaking for semiconductors - bringing them together opens doors to building state-of-the-art electronics including gear that’s all about harnessing the power of light.
- Minimal Thermal Stress : Cool temps are the secret here—not reaching the melting points keeps everything stable and straight, protecting those intricate semiconductors we rely on every day from any kind of damage or distortion.
Challenges
- Surface Cleanliness : Achieving the necessary level of surface cleanliness and smoothness is challenging and critical for successful diffusion bonding.
- Precise Temperature and Pressure Control : Getting the temperature and pressure just right is key for things to mix and stick properly.
What is Atomic Diffusion Bonding?
Atomic diffusion bonding is a high-precision joining process used to create strong, cohesive bonds between materials at the atomic level without melting them. It relies on the principle of atomic diffusion, where atoms migrate across the interface of the materials being joined. This process is particularly important in applications requiring high strength and minimal deformation, such as in aerospace, microelectronics, and advanced manufacturing.
Key Steps in Atomic Diffusion Bonding
- Surface Preparation: The surfaces to be bonded are meticulously cleaned and polished to ensure they are free from contaminants and have an atomic-level smoothness.
- Alignment and Clamping: The prepared surfaces are precisely aligned and clamped together under pressure to maintain intimate contact.
- Heating: The assembly is heated to a temperature below the melting point of the materials. This temperature is high enough to facilitate atomic diffusion but not high enough to cause melting.
- Holding: The temperature and pressure are maintained for a specified duration, allowing atoms to migrate across the interface and form a strong bond.
Advantages of Atomic Diffusion Bonding
- High Strength and Integrity: The bonds formed are often as strong as the parent materials, providing excellent mechanical properties.
- Minimal Deformation: Since the process occurs below the melting point, there is little to no deformation of the parts being joined.
- Capability to Join Dissimilar Materials: This process allows the bonding of materials that may be difficult to weld using traditional methods.
- Precision: Atomic diffusion bonding can achieve very high dimensional accuracy, making it suitable for precision engineering applications.
Applications
- Aerospace: Used for joining components in jet engines, airframes, and other high-stress environments.
- Microelectronics: Employed in the fabrication of microelectromechanical systems (MEMS) and integrated circuits where precision and reliability are critical.
- Medical Devices: Used in the production of implants and surgical instruments where biocompatibility and strength are essential.
- Optoelectronics: Applied in the bonding of materials for LEDs, laser diodes, and other photonic devices.
Process Considerations
- Surface Cleanliness: Achieving the necessary level of surface cleanliness is crucial for successful bonding, as contaminants can inhibit atomic diffusion.
- Precise Temperature and Pressure Control: Maintaining exact temperature and pressure conditions is essential to ensure proper diffusion and bonding.
Conclusion
Atomic diffusion bonding is a sophisticated and highly reliable technique for creating high-strength, high-integrity bonds between various materials. Its ability to join materials at the atomic level makes it indispensable for advanced applications requiring precision, strength, and durability.