4H and 6H Silicon Carbide (SiC) Wafers
A PhD candiate requested a quote for SiC substrates. Click here how we help researchers with custom SiC requests.
We are interested on these wafers. We would like to know more information about these wafers such as thickness, Silicon Carbide type (4H or 6H) and orientation.
1. General price of 2" SiC
2. General price of 3" SiC
3. General price of 4" SiC
4. General price of 6" SiC
We have got an university discount in our past purchases. Is that possible this time? That would really help us to purchase more wafers. We would like to get a few wafers and test if the broken areas affect our research. If they work fine we will purchase many more. So this is the initial list for the quote:
Reference #247746 for more specs and pricing.
Get Your Quote FAST! Or, Buy SiC Online and Start Researching Today!
Broken SiC Substrates For Researchers
We help budget constrained researchers souce the substrates that they need at an affordable price. Below see how we helped the University of Arizona School for Engineering of Matter, Transport and Energy.
We would like to get a few wafers and test if the broken areas affect our research. If they work fine we will purchase more. As a university lab we have a limited budget.
Could you please add to the quote the wafer characteristics such as thickness, type (4H or 6H) and orientation? This is the initial list (if possible) for the quote:
UniversityWafer, Inc quoted:
- (4 units) 2" SiC : thickness 350um, Polytype 4H, Orientation <0001> on-axis
- (1 unit) 3" SiC : thickness 350um, Polytype 4H, the orientation <0001> 4deg off-axis
Silicon Carbide (SiC) Wafers
Save and buy diced SiC wafers. In stock for an excellent price!
5x5mm, 6x6mm, 10x10mm 6H wafers and 5x5, 10x10, and 2" diameter 4H wafers in stock.
All of these SiC wafers are N-type, resistivity ~0.1-0.01 Ohm.cm
For 4H SSPwafer 10x10mm and 5x5mm
For 6H SSP wafer 10x10mm and 5x5mm
Below are just some SiC substrates available. Let us know what specs you can use or send us your own specs and quantity.
No.1
2" 6H N-Type
6H-N 2" dia,
Type/ Dopant : N / Nitrogen
Orientation : <0001>+/-0.5 degree
Thickness : 330 ± 25 um
D Grade,MPDä100 cm-2 D Grade,RT:0.02-0.2 Ω·cm
Single face polished/Si face epi-ready with CMP,Surface Roughness : <0.5 nm
No.2
2" 6H N-Type
6H-N 2" dia, Type/ Dopant : N / Nitrogen
Orientation : <0001>+/-0.5 degree
Thickness : 330 ± 25 um
B Grade,MPDä30 cm-2 B Grade,RT 0.02 ~ 0.2 Ω·cm
Single face polished/Si face epi-ready with CMP,Surface Roughness : <0.5 nm
No.3
2" 4H N-Type
4H-N 2" dia, Type/ Dopant : N / Nitrogen
Orientation : <0001>+/-0.5 degree
Thickness : 330 ± 25 um
D Grade,MPDä100 cm-2 D Grade:RT:0.01-0.1 Ω·cm D Grade,Bow/Warp/TTV<25um
Single face polished/Si face epi-ready with CMP,Surface Roughness : <0.5 nm
No.4
2" 4H N-Type
4H-N 2" dia, Type/ Dopant : N / Nitrogen
Orientation : <0001>+/-0.5 degree
Thickness : 330 ± 25 um
B Grade,MPDä30 cm-2 B Grade:RT:0.01 - 0.1 Ω·cm B Grade,Bow/Warp/TTV<25um
Single face polished/Si face epi-ready with CMP,Surface Roughness : <0.5 nm
No.5
3" 4H N-Type
4H-N 3" dia, Type/ Dopant : N / Nitrogen
Orientation :4 degree+/-0.5 degree
Thickness : 350 ± 25 um
D Grade,MPDä100 cm-2 D Grade,RT:0.01-0.1Ω·cm
D Grade,Bow/Warp/TTV<35um
Double face polished/Si face epi-ready with CMP,Surface Roughness : <0.5 nm
No.6
3" 4H N-Type
4H-N 3" dia, Type/ Dopant : N / Nitrogen
Orientation : 4 degree+/-0.5 degree
Thickness : 350 ± 25 um
B Grade,MPDä30 cm-2 B Grade,RT:0.01 - 0.1Ω·cm
B Grade,Bow/Warp/TTV<35um
Double face polished/Si face epi-ready with CMP,Surface Roughness : <0.5 nm
No.7
3" 4H SI
4H-SI 3" dia, Type/ Dopant : Semi-insulating / V
Orientation : <0001>+/-0.5 degree
Thickness : 350 ± 25 um
D Grade,MPDä100 cm-2
D Grade,RT:70 % ≥1E5 Ω·cm
Double face polished/Si face epi-ready with CMP,Surface Roughness : <0.5 nm
No.8
3" 4H SI
4H-SI 3" dia, Type/ Dopant : Semi-insulating / V
Orientation : <0001>+/-0.5 degree
Thickness : 350 ± 25 um
B Grade,MPDä30 cm-2 B Grade,RT:80 % ≥1E5 Ω·cm
Double face polished/Si face epi-ready with CMP,Surface Roughness : <0.5 nm
No.9
2" 6H SI
6H-SI 2" dia, Type/ Dopant : Semi-insulating / V
Orientation : <0001>+/-0.5 degree
Thickness : 330 ± 25 um
D Grade,MPDä100 cm-2 D Grade,RT:70 % ≥1E5 Ω·cm
Single face polished/Si face epi-ready with CMP,Surface Roughness : <0.5 nm
No.10
2" 6H SI
6H-SI 2" dia, Type/ Dopant : Semi-insulating / V
Orientation : <0001>+/-0.5 degree
Thickness : 330 ± 25 um
B Grade,MPDä30 cm-2 B Grade,RT:85 % ≥1E5 Ω·cm
Single face polished/Si face epi-ready with CMP,Surface Roughness : <0.5 nm
No.11
4" 4H N-Type
4H-N 4"dia.(100mm±0.38mm),
Type/ Dopant : N / Nitrogen
Orientation : 4.0°±0.5°
Thickness : 350μm±25μm
D Grade,MPDä100 cm-2
D Grade,0.01~0.1Ω•cm
D Grade,TTV/Bow /Warp<45um
Double face polished/Si face epi-ready with CMP, Surface Roughness: <0.5 nm
Broken Silicon Carbide as Cleaving Substrates
Broken Silicon Carbide, an inexpensive alternative.
Do you still have any Broken SiC with the following specifications? Following up on your quote for broken SiC below. We're interested in ordering a few of the 3" wafers, 700 um thickness. Also, what volume discounts can you offer if we buy more than a few? Any offers for quantities of 5 or 10?
- 3" Broken SiC : thickness 500 (or 700) +/-25um,4H,the orientation <0001> 4deg off-axis
- 4" Broken SiC : thickness 500+/-25um,4H,the orientation <0001> on-axis (or 4deg off-axis)
The 2" Broken SiC we bought in the past worked perfectly fine for our purposes. We are using them as cleaving substrates. We cleave thin wafers out of them.
Electronic devices made from Silicon carbide (SiC) wafers can operate at a high power, high heat and deadly doses of radiation than traditional silicon.
SiC Wafer Applications Include:
- Jet Engines where extreme heat is a problem for silicon.
- Wireless chips
- Radar
- Smart devices for autos
Silicon Carbide Electric Vehicle Applications
Silicon carbide has several benefits, making it a perfect choice for high-performance electric vehicle applications. In short, it has a wider bandgap than silicon, enabling it to handle higher voltages without degrading. In addition, silicon carbide is cheaper to operate than silicon. If these attributes are important to you, then you should consider purchasing a silicon carbide electric vehicle. Here's a closer look at this exciting material.
Silicon Carbide Can Discharge Larges Amounts of Energy
The future of the electric vehicle depends on the ability to store and discharge large amounts of energy. But SiC is not limited to EVs. It is also used in clean-energy devices, ubiquitous HVAC systems, and industrial motors. SiC is more efficient than silicon and helps reduce heat and losses. The market for silicon carbide is projected to grow at double-digit rates between 2019 and 2026. And while SiC may not yet be a viable replacement for the battery of an EV, it is poised to become a key technology for EVs.
While silicon is a better material for the battery in electric vehicles, it is more expensive. This is one reason why silicon carbide is more expensive. It is difficult to produce SiC, and is expensive. However, it can be made more efficient than silicon. The difference is about six percent. SiC has an advantage over silicon because it has higher operating temperatures and can squeeze out more energy. It can be used in electric vehicle batteries with large capacities.
Silicon Carbide Has a Wider Bandgap
The Silicon Carbide semiconductor is a great choice for battery and inverter applications for electric vehicles. It is a low-emissions, wide-bandgap semiconductor. There are some challenges associated with its use in electric vehicles, though. While SiC's bandgap is larger than Gallium Nitride (GaN's), it's still a good candidate for automotive applications. However, as the technology advances and is more widely used, the automotive industry may be forced to make some decisions.
Wider bandgap semiconductor materials have many advantages over Si. The bandgap is the amount of energy a semiconductor can store or release in a certain temperature range. The higher the bandgap, the lower the breakdown voltage. For this reason, SiC is often used for automotive applications, where a high voltage is required. It also exhibits a self-biasing feature when overvoltage is detected.
Silicon Carbide is Cheaper to Operate than Silicon
Silicon carbide is an excellent material for controlling electric current. It has a wide band gap that allows electrons to flow freely and presents less resistance in conducting mode. This can translate to greater power from a battery. Silicon carbide's high-performance properties can also be applied to solar and wind power systems, industrial motors, and HVAC systems. The next step for silicon carbide is electric vehicle applications.
Because SiC is so durable and cheap to make, automakers and Tier-1 suppliers are now using it to build and operate higher-voltage batteries. SiC will save automakers and Tier-1 suppliers up to $750 per unit. This material is now cheaper to operate than other materials and is expected to grow in the coming years. Silicon carbide has a double-digit compound annual growth rate over the next two to three years.
Silicon Carbide Can Withstand Higher Voltages
The latest breakthrough in silicon semiconductor technology is an electrical component that can withstand higher voltages and higher temperatures. Silicon carbide devices have been undergoing research for automotive powertrain applications. They differ from silicon in several ways, including their electrical properties and thermal conductivity. SiC is suited to higher voltages, can operate at higher temperatures, and can be cooled more efficiently. SiC also has higher energy efficiency.
The advantages of silicon carbide in electric vehicle applications go beyond EVs, however. The market for this material is much larger than EVs, and encompasses numerous clean-energy devices and ubiquitous HVAC systems. Industrial motors are an example of these, as they run 24/7 and are often much larger than automotive motors. The higher voltages that SiC can withstand make them a superior conductor.
Video: Charge Electric Vehicles with SiC
Why Use Silicon Carbide Semiconductors?
Silicon carbide (SiC) semiconductors are a type of semiconductor that is gaining popularity, particularly in high-power, high-temperature, and high-frequency applications. Silicon carbide has several beneficial properties that make it a strong contender in these areas compared to traditional silicon (Si) semiconductors.
Here are some characteristics of silicon carbide semiconductors:
-
High Temperature Tolerance: Silicon carbide has a higher thermal conductivity than silicon, meaning it can handle higher temperatures. This makes it suitable for use in devices that are exposed to high temperatures or need to dissipate a lot of heat.
-
High Power Efficiency: Silicon carbide has a larger bandgap than silicon, meaning it requires more energy to switch from an insulator to a conductor. This allows SiC devices to handle high voltage levels more effectively, resulting in more efficient power conversion.
-
High Frequency: Silicon carbide's larger bandgap also makes it useful in high-frequency applications. SiC devices can operate at higher frequencies without losing as much energy in the form of heat.
-
Radiation Resistance: Silicon carbide is more resistant to radiation than silicon. This makes it attractive for use in space applications, where devices are exposed to high levels of radiation.
Because of these properties, silicon carbide semiconductors are often used in power electronics, such as in inverters for electric vehicles or solar power systems, as well as in radio frequency (RF) devices like radar systems. However, as of my knowledge cut-off in September 2021, SiC technology is still being developed and is not as mature or widespread as traditional silicon technology. Nevertheless, the advantages of SiC make it a promising material for future semiconductor devices.
Silicon Carbide Semiconductors Suppliers
Silicon carbide semiconductor is a unique material that can handle high temperatures, high voltages and lower power losses. It can also process electricity more efficiently than traditional semiconductors in many important applications.
It is a robust compound of silicon and carbon with a hexagonal structure. It has wide band-gap semiconductor properties, which means electrons need less energy to move through it than in silicon.
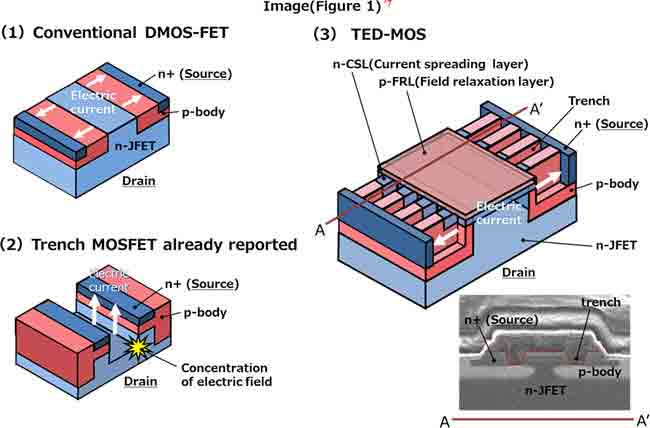
On Semiconductors
Semiconductors are the building blocks of electronic systems and essential to most modern devices. They are also critical to industries such as automotive, energy and consumer electronics, and are considered a strong indicator of the health of the economy. Silicon is currently the dominant semiconductor material, but other alternatives are rapidly gaining traction. One such alternative is silicon carbide. This material has the potential to revolutionize several markets by enabling power-efficient electronics.
Silicon carbide (SiC) semiconductors offer higher electrical field strength breakdown and wider band gap than conventional silicon power semiconductors. These features enable them to withstand higher temperatures and voltages, resulting in lower on-state losses and switching loss. These advantages make SiC semiconductors ideal for power conversion applications, especially those in the e-mobility, energy and industrial sectors.
In the automotive market, SiC semiconductors can improve vehicle efficiency and range by reducing power loss in electric vehicles. The technology can allow for faster charging, reduce battery size and weight, and increase vehicle power output. It can also help cut fuel consumption by up to 20%, which is good for the environment and for drivers’ wallets.
Moreover, the use of silicon carbide in automobiles can reduce the amount of CO2 emissions generated by vehicles. The demand for electric cars is increasing, and the technology can help meet that demand while improving the vehicles’ safety, comfort, and performance.
The market for SiC semiconductors is expected to grow significantly in the coming years, as demand for electric cars rises and governments encourage their use. SiC chips are expected to replace silicon-based semiconductors in electric vehicle power management ICs, which control the flow of current to and from the motor. They are also used in the traction inverters that convert electrical power into mechanical torque for the wheels.
A number of companies are working to develop and manufacture silicon carbide semiconductors, including Onsemi. The company is making strategic acquisitions to accelerate its development of these cutting-edge products. Its latest deal is a $415 million purchase of GT Advanced Technologies. In addition, Onsemi is expanding its Hudson, New Hampshire facility and kicking off production of silicon carbide wafers in the Czech Republic.
Infineon Technologies
Silicon carbide (SiC) semiconductors reduce power loss and generate less heat, thereby conserving energy. They also work at higher switching frequencies than conventional silicon-wafer power semiconductors. This allows for system size reduction and power density increases, and they offer long-life reliability. In addition, SiC devices are more environmentally friendly than their silicon counterparts.
Infineon Technologies is a leading global manufacturer of microelectronics. The company provides a comprehensive portfolio of products, solutions, and services to drive digitalization of the economy and society. The company’s products include integrated circuits for automotive and industrial applications, memory chips for mobile computing, digital security, and advanced microcontrollers. Infineon has a strong presence in Asia, Europe, and the United States.
The company’s CoolSiC(tm) MOSFET power modules enable designers to realize never-before-seen levels of efficiency and power density. These high-temperature and harsh-environment semiconductors are based on state-of-the-art trench semiconductor processes, which allow for the highest efficiency at the highest operating temperatures. They are ideal for hard-switching topologies, such as LLC and ZVS, and can be easily driven with gate driver ICs.
Recently, Infineon Technologies and Foxconn Technology Group signed a Memorandum of Understanding to work together on the development of innovative silicon carbide power semiconductors for advanced electromobility. The companies plan to develop a platform that supports the entire vehicle lifecycle, from battery management systems to traction inverters. The collaboration combines Infineon’s expertise in automotive SiC power semiconductors with Foxconn’s manufacturing and design capabilities.
Infineon Technologies has a long-term agreement with Chinese SiC supplier TanKeBlue to secure competitive and high-quality 150-millimeter wafers and boules for the production of SiC power semiconductors. This will contribute to supply chain stability, particularly with regard to the growing demand for SiC devices in EV charging and solar power applications. In addition, the company has a partnership with Resonac to provide intellectual property rights relating to SiC materials. This will enable it to support rapid growth of the emerging market for SiC devices. The two companies are also establishing a system application center to optimize the integration of automotive solutions into vehicles. This will enable them to address key customer demands such as intelligent driver assistance, smart cabin and battery management systems.
STMicroelectronics
STMicroelectronics (STM) is one of the world's top semiconductor companies. Its devices are used in everything from cell phones to advanced industrial control systems. Its manufacturing facilities are located in Europe, Asia, and North America. In addition, it has several design centers in various parts of the world. The company's headquarters are in Switzerland. It is listed on the Paris and New York stock exchanges. In 1994, SGS Thomson became STMicroelectronics after its initial public offering on the stock market. In 2000, the company moved its headquarters from France to Switzerland. In 2004, STMicroelectronics acquired Motorola's semiconductor business, which it had previously owned jointly with TSMC. This acquisition allowed the company to increase its market share and global footprint. In 2022, STMicroelectronics announced that it would invest 7.5 billion euros ($9.3 billion) in a chip factory in Crolles, southeastern France. The French government will provide 2.9 billion euros ($3.10 billion) in state aid to help support the investment.
The silicon carbide device market is expected to grow significantly in the coming years. Increasing demand for electric vehicles and renewable energy will drive demand for these devices. The high efficiency and power density of silicon carbide devices allow for smaller, more compact systems. These devices are also more reliable than silicon-based alternatives.
As the market for silicon carbide devices grows, STMicroelectronics is expanding its production capacity to meet demand. It is investing in a joint venture with Sanan Optoelectronics, which will produce silicon carbide devices exclusively for ST. These devices are used in electric vehicle inverters. They lower power losses and enable EVs to charge more quickly and travel farther than they would otherwise be capable of.
In 2025, STMicroelectronics will begin supplying silicon carbide devices to ZF, an automotive supplier. These devices will be integrated into the modular inverter design that ZF plans to use in its elect ric cars. The devices will be manufactured by ST at production facilities in Italy and Singapore and packaged into STPAKs, an innovative package designed by the company. They will then be tested at back-end facilities in Morocco and China.
Silicon Carbide
Silicon carbide (SiC) is a hard, crystalline chemical compound that contains both silicon and carbon. It occurs naturally as the rare mineral moissanite and has been mass-produced as a powder since 1893 for use as an abrasive. Grains of SiC can be bonded together using sintering to form very hard ceramics that are used in applications that require high endurance, such as car brakes and bulletproof vests. It can also be cut into gemstones known as synthetic moissanite. SiC is also a key ingredient in the carborundum printmaking process – a type of collagraph printmaking that uses grit to create inked prints on paper.
The market for semiconductor devices is booming. These devices are used in a wide variety of electronic and power applications, including electric vehicles, aerospace & defense, data & communication and energy & power. The technology behind these devices has pushed many industries to new heights. These technologies are revolutionizing the way we live and work. This has enabled us to make our lives easier and more comfortable. It has also benefited the economy by making it possible to operate businesses more efficiently.
A silicon carbide sic semiconductor device combines silicon (atomic number 14) and carbon (atomic number 6). The strong covalent bonds of these two elements result in a robust material that has high electrical and thermal conductivity. It also has a large bandgap, which is almost three times larger than that of silicon. This allows it to offer higher switching speeds and greater power density in a smaller device.
This third-generation core material is a great alternative to the first-generation materials of silicon and gallium arsenide. It offers superior performance over those materials in terms of current and voltage rating, power density, switching speed and temperature. These benefits are expected to drive the market for SiC in the near future.
Silicon carbide semiconductors are available in both ICs and discrete devices. They are also offered in a wide range of package types. They can be found in everything from LED drivers to automotive semiconductors. The best manufacturers of silicon carbide semiconductors are those that combine innovation with responsibility. They strive to provide their customers with the best products on the market. This is what makes them different from their competitors.
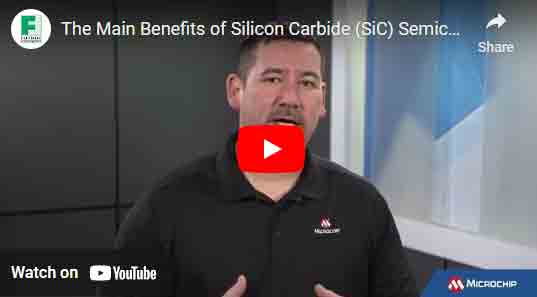
Five Pros and Cons of Silicon Carbide Substrate Properties Used to Fabricate Semiconductor Devices
Silicon carbide (SiC) is an attractive material for many applications due to its excellent physical and electronic properties. However, like any material, it also has limitations. Below are some of the advantages and disadvantages when used for the fabrication of semiconductor devices.
Advantages:
-
Wide Bandgap: SiC has a bandgap of 3.26 eV, significantly larger than silicon's 1.12 eV. This wide bandgap enables SiC devices to operate at high temperatures and high voltages.
-
High Thermal Conductivity: SiC's high thermal conductivity allows it to better dissipate heat, making it ideal for high-power applications.
-
High Electric Field Breakdown: SiC can withstand higher voltages before breaking down, which makes it ideal for power electronic devices.
-
High Saturated Electron Drift Velocity: This property allows devices to operate at higher frequencies, making SiC suitable for high-frequency applications such as RF and microwave devices.
-
Radiation Hardness: SiC is more resistant to radiation than silicon, making it useful in environments with high radiation levels, such as space applications.
Disadvantages:
-
Material Quality: As of my last update in 2021, despite significant improvements, SiC still doesn't quite match the material quality of silicon, with defects and impurities that can impact device performance.
-
Fabrication Costs: The production process for SiC wafers is more complex and costly than for silicon, which can drive up the cost of SiC-based devices.
-
Limited Size of Substrates: SiC substrates are typically smaller than their silicon counterparts, which can limit the number of devices that can be fabricated on a single wafer.
-
Complex Processing: The fabrication of SiC devices requires unique processing steps, which can be more complex and challenging than those for silicon devices.
-
Limited Maturity of Technology: Silicon technology is very mature, with a vast amount of research, development, and industrial knowledge available. In contrast, SiC technology is still relatively new and not as well understood. This can limit its adoption and the speed at which improvements can be made.