How to Determine the Price of a Silicon Wafer
Having the right information is crucial to determine the price of a silicon wafer. There are many factors to consider, including the cost per die, size, density, usable area rate and dopants. With all this information, you can decide if you want to purchase the product or not.
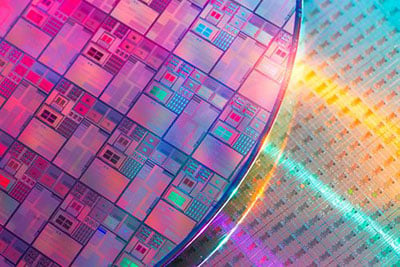
Wafer Size
Having a large silicon wafer size will reduce the cost per die. In addition to lower die cost, the larger size will help with production efficiency. The larger size will also reduce the cost per watt and increase the power output at the module level.
Silicon wafers are a popular material used in semiconductor manufacturing. They are used for making integrated circuits (ICs). These wafers are available in different sizes, ranging from a one-inch diameter to a 12-inch diameter.
The cost of making a silicon wafer varies depending on the following specs:
- Diameter
- Type/Dopant
- Orientation
- Resistivity
- Thickness
- Polish - Single or Double Side and surface thickness variation and flatness
- Grade
- How the ingot is grown CZ or FZ
- Volume - lower volumes on average cost more than higher volumes
- What kind of cassettes the wafers are packaged in hard or soft.
The cost of manufacturing a standar four-inch 500-um wafer can vary from just a few dollars per up to $32.00 per wafer. A a six-inch wafer can costs under $10.00/wafer to well over $100.00 per wafer. A 12-inch wafer costs a maximum of $5000, while an eight-inch one is priced at approximately from under ten dollars to $200 per wafer.
Increasing the size of silicon wafers is a trend that is expected to continue in the future. This is because larger wafers will offer a lower cost per die and higher throughput. Increasing the size of wafers also helps to reduce the cost of manufacturing ICs and modules, which is particularly useful in the solar industry.
In the semiconductor industry, the cost of making a silicon wafer depends on several factors, such as the diameter and thickness of the wafer, as well as the specifications for the wafer. Manufacturers need to maximize the number of complete dies per wafer.
The process of manufacturing silicon wafers involves many complex steps. These steps include photolithographic patterning, ion implantation, and deposition of various materials. The process of deposition includes thin film deposition, which imparts electrical and optical properties to the wafer. The thickness of the thin film is measured before and after the deposition process. This can be done with a chemical or physical method.
Substrate Density
Using defect concentration assessment to understand the technical capability of a semiconductor manufacturing process is essential. The determination of the defect concentration of each conductive layer on each chip is a critical step in the semiconductor manufacturing process. In order to improve the accuracy of defect concentration assessment, a defect concentration correction formula is developed.
This formula combines the theoretical defect density calculation model with the fatal defect rate coefficient. Using this formula, the defect concentration of each wafer produced can be obtained. This formula is a preferred method for defect concentration assessment in semiconductor package product packaging lines.
A silicon wafer is a thin piece of crystalline silicon that has been shaped and polished to form the substrate for a microelectronic device. This substrate undergoes many microfabrication processes to form individual microcircuits. This is then packaged as an integrated circuit.
Silicon is the most common semiconductor material and has a density of 2.33 g/cm3. It has a dielectric constant of 11.7 and an energy gap of 1.12 eV. Its thermal conductivity is 1.31 W/cmdegC.
Silicon wafers are commonly made in two different shapes: (100) or (111) faces. In addition, silicon wafers over 200 mm in diameter have flats cut along one or more clevage planes. These flats typically indicate the orientation of the wafer crystal.
The critical defect rate coefficient C is used in defect concentration calculation formulas to determine the wafer defect density. The formula includes the ratio of the effective chip count to the die area. This ratio is scaled by a polynomial factor to determine the chip count defect concentration.
The present invention has the objective of achieving a higher defect density and higher production yield. It includes a defect density correction calculation formula, which can be used to calculate the defect concentration of the wafer production line. This formula can also be used to predict the wafer yield value.
Usable Wafer Area Rate
Increasing the number of dies per wafer increases the number of chips per wafer. This is important in terms of throughput and lower cost per die.
However, increasing the number of dies per wafer requires significant engineering. In addition, there are issues regarding the metrology and orientation of the wafer. As a result, there may be limits to productivity increases.
Increasing the number of dies per wafer is one of the state-of-the-art challenges in the semiconductor industry. There are other issues that must be addressed in order to ensure the sustainability of capital investment.
These include surface defects. The detection of surface defects is one of the state-of-the-art technical challenges. As a result, development of instrumentation and effective testing is required.
Another critical concern is the functional dependence of size. As a result, it is important to determine the maximum die count per wafer. This is dependent on the size of test structures, die scribe lines, and die aspect ratio.
The number of dies per wafer also depends on the number of squares per square inch of the wafer. This number is derived from the circle area formula. In addition, the die count is dependent on the width of the scribeline and the kerf plus tolerance.
Similarly, the number of chips per wafer is also related to the number of squares per square inch. The number of chips per wafer is calculated using a polynomial factor. The number of chips per square inch varies among different foundries.
Finally, the number of dies per wafer can be calculated by multiplying the number of dies by the diameter of the wafer. This is similar to the number of chips per square inch, but is less exact.
Cost per die
Several years ago, the cost per die of a silicon wafer was an important factor in the growth of the industry. But recently, cost per die has dropped considerably.
Cost per die of a wafer depends on many factors, including the type of process used to create it. More complex processes are more expensive and require more capital investment. In order to create a high quality wafer, it is essential to use a pure material and to follow a strict testing process.
Some types of silicon wafers are manufactured by the Czochralski process, which involves pulling a seed crystal from molten silicon and forming a cylindrical boule. Other processes are less expensive.
The cost per die of a wafer is calculated using a formula. It is based on the number of dies produced from a wafer, the diameter of the die, and the number of layers.
For example, a four-inch 500-um wafer costs $27 when doped with phosphorus and $32 when doped with boron. A 20-cm wafer costs $15. It contains 100 dies.
More chips can be processed on a wafer, so the cost per die is lower. This is a good thing, because it allows more chips to be processed in the same amount of time. But it also means more processing equipment and materials are required.
Several process steps enable multiple wafer processing, and the cost per die of a wafer can decrease as the amount of money spent increases. But defect free silicon costs remain $567 for a monolithic product.
The number of layers and defects on the wafer also affects the cost per die. A single wafer can have up to fourteen EUV layers. The area of the wafer can be increased by 15% to increase defect density.
Dopants
Various materials can be used for making semiconductors. These materials include dopants, which are added to silicon to increase its conductivity. A doped silicon wafer can be formed by thermal ionization or by diffusion. During thermal ionization, free charge carriers are formed in both the conduction and valence bands.
The amount of dopants used to form the semiconductor is influenced by the temperature and the flow rate of dopant precursors. It is also influenced by the number of atoms of the dopant. A wafer with a high number of atoms of dopant is known as heavily doped. This type of semiconductor is widely used in CMOS technology and sensistors. It also shows a more linear positive thermal coefficient.
The most important factor influencing the doping concentration is the injection level. If the injection level is too low, the doping concentration will be lower than the set value. This causes measurement errors. In addition, the reflection of emitted photons will affect the concentration. Increasing the modulation frequency can also reduce the measurement error.
Photon reabsorption is used to measure the silicon doping concentration. PCR signals are detected on the front and rear surfaces of the wafer. The measured fit profile shows deep peaks in the doping atom concentration. PCR amplitude measurements are performed using a lock-in amplifier.
The spectral response of the PMT detector is from 700 nm to 1800 nm. A periodic intensity-modulated super-bandgap laser can also be used. The excitation wavelength is estimated at 40.5 s. In addition to the spectral response, the noise can also be analyzed by adding different levels of noise.
A wafer can be divided into dozens of individual circuit elements. The cost of a wafer depends on its size. Doping concentration will be lower with larger wafers.
Video: Cost of an Integrated Circuit