What Is Thin-Film Interference?
Thin-film interference occurs when light waves reflected from the top and bottom surfaces of a thin film interfere with each other, either constructively or destructively, based on their phase differences. This phenomenon is responsible for the vivid colors seen in oil slicks on water, soap bubbles, and various thin coatings. In micro and nanofabrication, thin-film interference plays an important role in fields like MEMS (Micro-Electro-Mechanical Systems) and optical coatings.
Here’s a breakdown of key concepts:
1. Conditions for Interference
- Film Thickness: For interference to be noticeable, the film’s thickness should be on the order of the wavelength of visible light (around 100-300 nm).
- Refractive Index Contrast: Differences in refractive indices between the film, substrate, and surrounding medium (often air) are essential. Higher contrasts amplify interference effects.
- Light Path Difference: The light path difference between the two reflecting surfaces causes phase differences that determine constructive (bright) or destructive (dark) interference.
2. Constructive and Destructive Interference
- Constructive Interference: Occurs when the path difference equals an integer multiple of the wavelength (2nt=mλ2nt = m\lambda 2nt = mλ), making the film appear bright at specific wavelengths.
- Destructive Interference: Occurs when the path difference is an odd multiple of half the wavelength (2nt=(m+0.5)λ2nt = (m + 0.5)\lambda 2nt = (m + 0.5)λ), creating dark bands or reducing the brightness at certain wavelengths.
Here, nn n is the refractive index of the thin film, tt t is the film thickness, λ\lambda λ is the wavelength of light in a vacuum, and mm m is an integer representing the order of interference.
3. Applications in MEMS and Optical Devices
- Optical MEMS: Thin-film interference is often used in optical MEMS devices to enhance or filter specific wavelengths, such as in coatings that control light transmission, reflection, or absorption.
- Microelectrodes and Sensors: Thin films in these devices can be used to create interference patterns that enhance sensitivity, enable colorimetric detection, or provide protective coatings with controlled optical properties.
Would you like to dive deeper into any specific applications of thin-film interference in your work with MEMS or other optical devices?
Sputtered Metal Deposition
We understand how important quality is to you. Our sputter process has been designed to deposit ultra-clean metal and dielectric films. All wafer processing, including metal deposition, is performed inside our class 100 clean-room. An in-situ RF etch is added to the process to insure good film adhesion and ohmic contact to underlying conductive layers.
In addition to an In-situ RF etch, we can provide an HF-dip just prior to sputtering aluminum and aluminum alloy films. Adding this additional step can further increase ohmic contact between layers.
Sputtered metal deposition is an omni-directional process. For this reason, sputter deposition is not a good candidate for Lift-Off processing. If you are interested in metal for Lift-Off processing please see our E-beam evaporation metals page.
All sputter films are available on silicon wafers sizes up to 300mm in diameter. We can also provide sputtered films on non-silicon materials, including quartz and glass wafers. We offer a wide variety of sputtered non-precious metals, dielectric films, and silicon. Precious metals are available for E-Beam evaporation.
- High purity Gold (Au) Target Purity 4N

- High purity Silver (Ag) Target Purity 4N

- High purity Platinum (Pt) Target Purity:3N5 and 4N

- High purity Aluminum (Al) Target Purity 4N, 5N and 5N5

- High purity Copper (Cu) Target 4N5 and 6N

- High purity Titanium (Ti) Target Purity: 2N7 and 4N5

- High purity Nickel (Ni) Target Purity: 3N5 and 4N5

- High purity Tantalum (Ta) Target Purity: 3N5 and 4N5

- High purity Tungsten (W) Target Purity: 3N5

- Molybdenum (Mo) Target Purity: 3N5

- High purity Silicon (Si) Target Purity: 4N, 5N and 6N

- High purity Graphite (C) Target Purity: 4N and 5N

- High purity Chromium (Cr) Target Purity: 3N5 and 3N8

- Magnesium (Mg) Target Purity: 3N5

- Germanium (Ge) Target Purity: 5N and 6N

How Do You Make Thin Film Solar Panels?
Making thin-film solar panels involves depositing layers of photovoltaic materials onto a substrate to capture sunlight and convert it into electricity. Here’s an overview of the main steps and materials used in thin-film solar panel fabrication:
1. Choose the Substrate
- Common substrates include glass, plastic, or metal foils. The choice depends on the application, flexibility requirements, and durability needed.
- Glass is widely used for rigid panels, while plastic and metal foils are popular for flexible or lightweight designs.
2. Select the Photovoltaic Material
- Amorphous Silicon (a-Si): Used for low-cost and flexible solar panels. However, it has lower efficiency than crystalline silicon.
- Cadmium Telluride (CdTe): One of the most common thin-film materials, offering high absorption and relatively good efficiency at low costs.
- Copper Indium Gallium Selenide (CIGS): Known for high efficiency and flexibility, although it’s more complex to manufacture.
- Perovskite: A newer material with potential for high efficiency and ease of production, though stability and scalability remain challenges.
3. Deposit the Thin-Film Layers
Each material requires different deposition methods, including:
- Chemical Vapor Deposition (CVD): Often used for depositing a-Si and other semiconductor materials.
- Sputtering: Common for CIGS and CdTe deposition, as it provides a controlled way to apply thin layers.
- Electrodeposition: A cost-effective technique used mainly for CIGS.
- Thermal or Physical Vapor Deposition (PVD): Useful for depositing metallic contacts and other layers.
The photovoltaic layer is usually between 1 to 2 micrometers thick, making it significantly thinner than traditional crystalline silicon wafers, which are around 150-200 micrometers.
4. Add Additional Layers
- Buffer Layer: Typically used to improve electron collection and prevent electron-hole recombination, especially in CdTe and CIGS cells. CdS is a common buffer layer material.
- Transparent Conductive Oxide (TCO) Layer: Acts as the front electrode, allowing light to enter while collecting electrical charges. Materials like indium tin oxide (ITO) or zinc oxide are often used.
- Back Contact Layer: Usually made from metals like molybdenum, this layer collects and transmits electrons to the external circuit.
5. Encapsulation
- Encapsulation protects the thin-film layers from environmental degradation (e.g., moisture, oxygen). EVA (ethylene-vinyl acetate) is commonly used for encapsulation, and a top glass layer or plastic sheet provides additional protection.
6. Testing and Quality Control
- Panels undergo rigorous testing to ensure they meet performance standards for efficiency, stability, and durability. Testing includes efficiency measurements under simulated sunlight, thermal cycling to test durability, and humidity resistance to check for moisture stability.
Advantages of Thin-Film Solar Panels
- Lightweight and Flexible: Some thin-film materials allow for flexible and lightweight panels, ideal for applications like building-integrated photovoltaics or portable solar systems.
- Lower Material Cost: Thin-film materials use less raw material and can be deposited over larger areas, often resulting in lower costs.
- Better Performance in Low Light: Some thin-film technologies perform better in low-light conditions or at high temperatures compared to traditional crystalline silicon.
If you're interested in further details on one of the materials or the specifics of a deposition method, I’d be glad to elaborate!
What Is a Thin Film Transistor?
A thin-film transistor (TFT) is a special type of transistor used in displays and other applications requiring thin, lightweight, and compact electronics. Unlike traditional bulk transistors that use crystalline silicon wafers as the semiconductor layer, TFTs are built by depositing thin films of semiconductor material on a non-conductive substrate (like glass or plastic). TFTs are widely used in flat-panel displays, such as LCDs (liquid crystal displays) and OLEDs (organic light-emitting diode displays), and in other devices that need a matrix of transistors for switching or amplifying signals.
Key Components and Structure of a Thin-Film Transistor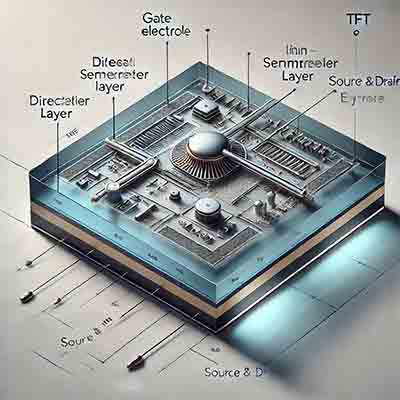
A TFT typically consists of the following layers:
-
Substrate:
- The substrate serves as the base layer and is usually made of glass or plastic. Glass substrates are more common in displays for their rigidity and transparency, while plastic substrates enable flexible and lightweight applications.
-
Gate Electrode:
- This layer controls the flow of charge in the transistor. The gate electrode is usually a thin metal layer deposited on the substrate and isolated from the semiconductor by an insulating layer (dielectric).
-
Dielectric (Insulating Layer):
- This layer, often made of silicon dioxide (SiO2) or silicon nitride (Si3N4), separates the gate electrode from the semiconductor layer. When a voltage is applied to the gate, an electric field is created that influences the flow of charge in the semiconductor.
-
Semiconductor Layer:
- The semiconductor layer is typically a thin film of amorphous silicon (a-Si), polysilicon, or increasingly organic semiconductors or metal oxides (like zinc oxide). This layer forms the conductive channel through which current flows when the transistor is "on."
-
Source and Drain Electrodes:
- These electrodes are metal contacts on either side of the semiconductor layer. When a voltage is applied to the gate, it allows current to flow from the source to the drain, enabling the transistor to act as an on/off switch.
Working Principle of a Thin-Film Transistor
When a voltage is applied to the gate electrode, it creates an electric field in the semiconductor layer. This electric field modulates the conductivity of the semiconductor, allowing or blocking the flow of current between the source and drain electrodes. The TFT essentially acts as a switch that turns on and off the current based on the gate voltage.
Types of Thin-Film Transistors
-
Amorphous Silicon (a-Si) TFTs:
- Most commonly used in standard LCD displays.
- Lower electron mobility than crystalline silicon but sufficient for applications like TVs, monitors, and low-cost displays.
-
Polycrystalline Silicon (Poly-Si) TFTs:
- Higher electron mobility than amorphous silicon.
- Used in high-resolution or small displays, such as smartphone screens and high-performance LCDs.
-
Metal Oxide TFTs:
- Materials like indium gallium zinc oxide (IGZO) offer high mobility and transparency.
- Used in advanced displays, including high-resolution OLED screens and transparent electronics.
-
Organic TFTs (OTFTs):
- Based on organic semiconductor materials, making them potentially flexible and lightweight.
- Applications include flexible displays, wearables, and other emerging electronic devices.
Applications of Thin-Film Transistors
- Flat-Panel Displays: TFTs are the basis for pixel control in LCDs and OLEDs. Each pixel in a display has its own TFT that controls the light output for high-resolution, high-contrast images.
- Flexible Electronics: With plastic substrates and organic semiconductors, TFTs can be used in flexible and foldable displays.
- Sensors and Wearables: TFTs are also used in thin, flexible sensors, making them suitable for biomedical wearables and environmental sensing.
Advantages and Limitations
Advantages:
- Allows high-resolution control of individual pixels in displays.
- Lightweight, thin, and compatible with large-area substrates.
- Can be manufactured on flexible substrates for emerging applications.
Limitations:
- Lower mobility in materials like amorphous silicon compared to crystalline silicon, which limits speed.
- May have stability and lifetime issues depending on the material, especially in flexible applications.
Would you like more information on a particular type of TFT or its application in a specific area?