Polysilicon Used in Research
Scientist Requested:
I am currently working on a project where the final goal is to develop a logic integrated circuit. For this, I would need to buy, if possible, a P-type wafer, with both the oxide layer (10nm) and a polysilicon layer deposited (>250nm), all to avoid the dangerous process of cvd for polysilicon deposition. I would like to know if you have any and if so, the price.
UniversityWafer Quoted
2" wafers SSP P-type wafer oxide layer (10nm) and a polysilicon layer deposited (>250nm)
Contact us for pricing. Reference #264057
Get Your Quote FAST! Or, Buy Online and Start Researching Today!
Polysilicon Researching Photovoltaics
I work on characterization of materials mostly used in photovoltaics. I came across to your company while looking for polycrystalline Si samples. Our research group needs a polycrystalline sample for some optical measurements to tackle some research problems. Do your company manufacture polysilicon and if it does can you tell me about the polysilicon material? For example, the dimensions of the samples you offer, the grain size of the polycrystalline Silicon etc.
How Will US Tariffs on Chinese-made Solar Wafers and Polysilicon?
US tariffs on Chinese-made solar wafers and polysilicon are a contentious issue with a mix of economic, strategic, and environmental implications. Here’s an overview of the potential impacts and considerations:
Economic and Trade Dynamics
- Domestic Protectionism: The tariffs aim to protect the U.S. solar manufacturing industry from what has been described as unfair trade practices, such as subsidies provided by the Chinese government to its solar industry.
- Cost Implications: Tariffs increase the cost of importing solar wafers and polysilicon, potentially driving up the cost of solar panels for U.S. consumers and businesses. This could slow the adoption of solar energy in the short term.
- Impact on Global Supply Chains: Since China is a dominant player in the global solar industry, tariffs can disrupt supply chains and force U.S. manufacturers to seek alternative suppliers, possibly increasing lead times and costs.
Strategic Considerations
- Energy Independence: By encouraging domestic production, tariffs align with goals of increasing U.S. energy security and reducing reliance on foreign sources for critical materials.
- Technological Competition: The move is part of broader competition with China in high-tech industries, where control of critical technologies and materials like solar components is strategic.
Environmental Implications
- Renewable Energy Goals: Higher costs for solar installations could slow progress toward renewable energy targets, which are crucial for addressing climate change.
- Carbon Footprint: If domestic manufacturing capacity isn't sufficient to meet demand, reliance on other countries with less efficient or less environmentally friendly production processes might offset any gains from reduced imports from China.
Global Trade and Relations
- WTO Disputes: Tariffs can lead to disputes in the World Trade Organization (WTO) and escalate tensions in the broader U.S.-China trade relationship.
- Retaliation Risks: China might impose retaliatory measures, affecting other industries and products beyond solar materials.
Industry Response
- Increased U.S. Production: Some U.S. companies are scaling up domestic manufacturing to capitalize on the protectionist measures.
- Innovation: The tariffs might incentivize innovation in alternative materials or processes that reduce dependence on Chinese inputs.
The effectiveness of these tariffs depends on their ability to boost U.S. manufacturing capacity without unduly harming the solar market's growth and the pace of renewable energy adoption. Balancing protectionism with global cooperation is a persistent challenge in such policies.
Would you like insights on how this affects your sector or strategies to navigate it?
How Thick Can Polysilicon Be?
A PhD student requested a quote for the following.
I am looking of Polysilicon/SiO2/Si wafer. How thick can polysilicon be? what are the minimum and maximum thickness limits?
Would it be possible to get 4" silicon wafers? We typically work with p-type wafers, so they can serve as the substrate under the polycrystalline layer. As a first step, we would need probably 25 pieces.
We offer required film stack wafer 500nm Polysilicon/SiO2/Si wafer 100mm, P-type Boron doped, one side polished, 500+/-25um, 100 orientation
Reference #320415 for specs and pricing.
What Is Polysilicon Wafers?
Polysilicon, also known as multicrystalline silicon, is a common raw material for the electronics industry. Its feedstock is large rods that are broken into chunks of a specific size. The rods are packaged in clean rooms and directly cast into multicrystalline ingots. After these crystals are grown, the material is dried, and single crystal boules are cut into thin silicon wafers for semiconductor devices.
Polycrystalline Silicon, on the other hand, is the highest purity form of silicon. This type of silicon
has excellent insulating properties and a high temperature resistance. It begins as a granular or chunk form, and is often used for high-conformity and thin applications. The polysilicon is then doped with a variety of other elements, including aluminum, gallium, and magnesium. The levels of dopant, or additives, influence the material's resistivity.
Although polysilicon is an important building block for semiconductors, it has a low melting point. The melting point of the material is approximately 250°F. It is very difficult to make a polysilicon chip that is too hot. It is therefore advisable to keep the temperature at around 200°C. It is not feasible to manufacture devices with a lower temperature. In some applications, a low-temperature process can be used.
This type of polysilicon is a super pure form of silicon. It is highly resistant to temperature fluctuations and has great insulating properties. It is amorphous material that begins in a chunk or granular form. Granular Polycrystalline Silicon is used for thin applications, as it is easier to work with. It can be doped or not. The levels of dopant and resistivity are inversely proportional. Lightly doped Polycrystalline Silicon will have high resistivity, while a densely doped material will have low resistance.
Polysilicon is a type of nonmetallic material that can be used for various applications in electronics. It is a form of silicon that is very pure and contains no impurities. The polycrystalline form of silicon is widely used for solar PV cells. As a result, it is a vital raw material for electronic devices. The high purity of this material makes it a valuable product in many industries, from smartphones to semiconductors.
It is the most abundant form of polysilicon. Its purity is greater than one part per billion, which makes it the most common and most abundant material for the electronics industry. It is also a good source of silicon. Unlike solar cells, photovoltaic panels do not produce heat, but they absorb light and convert it into electrical energy. This makes the photovoltaic panels very efficient. They are an effective and low-cost alternative for those who are looking to generate renewable energy.
Almost all polysilicon is crystalline over its width. The characteristic grain size (d) of polysilicon is one of its main uses. Its grain boundaries separate adjacent grains. They are the center of recombination and serve as the interface between two crystals. Typically, d values are one micrometre in length. The material is a solid material that is used in electronics. It is often sold as a white or clear liquid.
In contrast to polycrystalline silicon, polysilicon is an ultra pure form of silicon. Its insulating and temperature-resistance properties make it an ideal material for solar panel cells and electronics. While the crystals are made of two different materials, the two types of polysilicon have similar uses. However, the former is used in semiconductors to produce light-sensitive devices. The latter is a material with good thermal and electrical conductivity.
Polycrystalline silicon is a highly pure form of silicon. It has excellent insulating and temperature-resistance properties. It is usually found in granular or chunk form. Granular polysilicon is often used in high-conformity applications. It can also be doped. Because the amount of dopant varies, a lightly doped Polycrystalline Silicon will have high resistivity. In addition to this, polycrystalline solar grade silicon is less pure than amorphous silicon material.
The production of polycrystalline silicon is a critical part of semiconductor technology. It is the main material used in semiconductors, and is a valuable component of many electronic components. The demand for polysilicon has been increasing for several years. Aside from making semiconductors, it is also used in a wide range of applications, from lighting to solar panels. But what is polysilicon? Its chemical composition is identical to that of silicon and makes it an ideal material for electronic products.
What Is Polysilicon Used For?
In the semiconductor industry, polysilicon is widely used. It is a common ingredient in solar panels and the raw material for polycrystalline silicon. The chemical process used to produce this material starts with the reaction of quartzite or sio2 with carbon in an arc furnace. The product is a semiconductor with an electrical resistance that lies between that of metals and insulators. It also has other properties that make it useful in a number of fields.
Polysilicon is a form of silicon that is hyper pure and has semiconductor-like properties. It is often
used as a feedstock material in solar energy applications. In particular, it is used in the fabrication of solar PV cells, as it is a precursor material. Crystallized silicon cells are manufactured by cutting thin slices of polysilicon from a single crystal or block. The process of manufacturing crystalline silicon cells depends on the type of polysilicon that is used.
While polysilicon is a common ingredient in solar cells and semiconductor devices, the vast majority of its demand is now for solar cells. This shift in demand has resulted in a steep drop in prices. It is now widely available for manufacturing solar cells and semiconductor devices. Its low price means that it is now much more affordable. What is polysilicon used for? What is polysilicon use for para: The price of polysilicon has been falling steadily for several years, and there are many applications for it in VLSI. It can be used as a gate electrode for MOS devices. It can also be used as a conductor or ohmic contact in shallow junctions. It is a versatile material that can be doped to provide the required electrical conductivity and resistance.
Today, polysilicon demand has become more concentrated in the semiconductor industry, with the semiconductor sector making up approximately 90% of the demand. In 1995, there were only 15 metric tons of polysilicon. In 2014, that number increased to nearly 280 metric tons, an increase of 1670%. In addition, the amount of polysilicon in the semiconductor industry has increased by two-fold. The semiconductor industry continues to grow.
Polysilicon is produced by the ion-implantation method. The polysilicon layer is crystalline over its entire width. Its characteristic grain size, or d, is characterized by its high melting point and low density. The resulting structure is highly porous, enabling the material to be recycled multiple times. This makes polysilicon an extremely environmentally-friendly material. If you have a cell that uses silicon, it can save you money.
Polysilicon is a versatile material. Its high melting point makes it a great candidate for a semiconductor. It has an excellent electrical conductivity, making it a popular choice for a gate electrode material in MOS devices. Its low melting point makes it a valuable material in the electronics industry. Its low cost makes it a great investment for the semiconductor industry. Its high melting point makes it incredibly valuable in this industry.
The process of in-situ deposition involves adding phosphine and diborane to the reactant gas. Then, polysilicon is deposited using the in-situ method. The materials are then processed in an in-situ method. The silicon is then cooled with a hot iron-oxide bath. The final product of this process is the solar cell.
The production of polysilicon is the second largest semiconductor industry in the world. It is used in a wide range of applications, including solar cells and batteries. The polysilicon used in solar panels is a crystalline material. It can be melted to form a single crystal, which is referred to as monocrystalline silicon. The monocrystalline silicon produced is the most efficient and cost-effective type of solar panel.
Polysilicon is a compound of silicon and quartz. It is used in a variety of applications. Its use in solar cells has increased dramatically. It has a wide range of applications. This chemical is an excellent alternative to cadmium. If it doesn't meet your needs, it can be recycled. And if you're looking for an in-situ process, you can also use it to produce glass and plastic.
The Differences Between Silicon and Polysilicon
The main difference between polysilicon and silicon is the structure of the silicon atoms. In 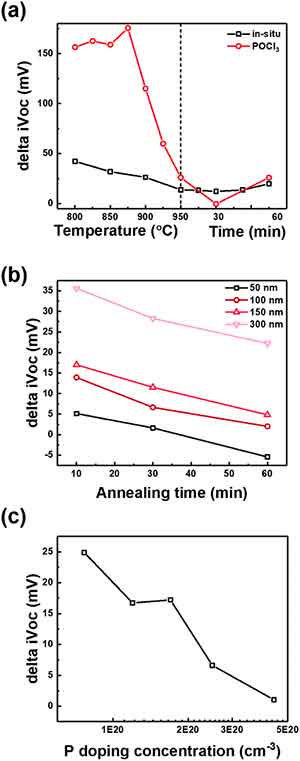
polysilicon, the atoms form a grain-like crystal. Each of the atoms is arranged in a regular pattern, and the grains typically range from 1,000 to 10,000 A. In amorphous silicon, the atomic structure is not discernible and the atoms are grouped in groups of four to six. In addition, the crystalline-like feature is absent, which makes it easier to process.
In monocrystalline silicon, the atomic structures are ordered and homogeneous. It is possible to recognize single crystals by their colour or even external colouring. However, large single crystals are rare in nature, and are difficult to produce in the lab. In contrast, amorphous silicon contains no crystalline order and a lack of grain boundaries. This structure has a high activation energy and is less durable than polycrystalline silicon.
Monocrystalline silicon is the most common form of Silicon. It is a continuous, homogeneous crystal that has no grain boundaries. These polycrystalline ingots are produced directly from raw material. A recrystallization process is then used to create single-crystalline boules, which are then sliced into thin silicon wafers for semiconductor devices. Amorphous silicon is not useful for electronics, however. It is also extremely hard to process in a laboratory.
What are Five Applications of Polysilicon Wafers
-
Solar cells: Polysilicon wafers are used as a base material for the production of photovoltaic cells in solar panels.
-
Semiconductors: Polysilicon wafers are used as the base material in the production of semiconductor devices, such as transistors, diodes, and integrated circuits.
-
MEMS: Microelectromechanical systems (MEMS) are used in various applications, such as pressure sensors, accelerometers, and gyroscopes, and are often manufactured using polysilicon wafers.
-
LED: Polysilicon wafers are used as a substrate material for light-emitting diodes (LEDs), providing a strong and stable base for the production of high-quality lighting devices.
-
Thin film transistors: Thin film transistors (TFTs) are used in displays, such as those found in laptops, smartphones, and televisions, and are often manufactured using polysilicon wafers.
Polysilicon wafers have a number of desirable properties, including high thermal stability, high electrical conductivity, and good mechanical strength, making them well-suited for use in a wide range of applications.