Diced Silicon Dies
A principal photonics engineer requested a quote for the following.
We require diced silicon die to the following specification. These will be used as precision mechanical spacers in test packages. This is an initial low quantity. If it goes well, we expect to need ~1000 die total in 2024, with 10x larger volumes to follow in 2025.
If this is a service that you offer, please quote as follows:
Please quote price and delivery for Quantity 20, 50 100
Specification
Silicon die
Thickness 1000+-25um
Length 7.900 +0 -0.050 mm Please note: 7.900mm is max acceptable length.
Width 4.850+-0.050 mm
Edges nominally 90 degrees to die surface
double side polish
no coating
doping type - don't care
orientation - don't care
growth type - don't care
Shipped in Gelpak or similar - please specify your typical package type.
Please indicate your typical specification for chipping, and for angle of diced edges.
Reference #280011 for specs and pricing,
Silicon Die Blue Tape
My client is interest in buying diced tape with silicon die attached (blue tape that contains minimum of 500mb nand flash). He is seeking to buy minimum of 100kg. Please let me know if you have that in stock and how much would it be? I've attached a photo of what we want in case I didn't describe it well enough =)
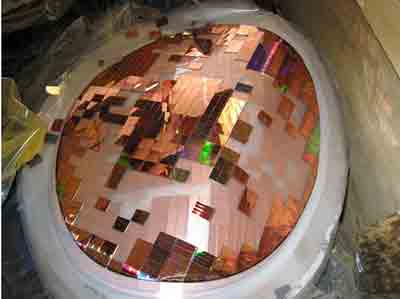
Metallized Silicon Dies
A graduate student requested a quote for the following.
We're working on a new research project and we need to know some technical data about the products you offer.
We need both type of silicon doped wafers (p & n). We need highly boron-doped and phosphor-doped wafers (i.e. 10^18 ? 10^19 cm^3).
- Do you have highly doped silicon wafers?
- What kind of doped silicon wafers do you have (ion implantation, diffusion or CZ)?
I have seen on your website that you can provide different silicon dice sizes and metallized silicon wafers.
- What is the smallest size of double sided metallized silicon dice?
- What kind of metals do you use for metallization?
Last but not least, what is the minimum order quantity?I have seen the size of the silicon wafers. I need to know the
smallest size of a double sided metallized silicon dice. We are
looking for a double sided metallized silicon die of approximately 4mm
x 4mm x ? mm.
Are you able to provide us with this kind of dice?
Reference #170102 for specs and pricing.
Thinned Silicon Dies
A Microelectronics Engineer at a large firm requested help with the following.
I would like to order some thinned and diced silicon die. Do not care about the doping or crystalline orientation. I would like the following dimensions:
QTY 5: 4 x 4cm die with 100um thickness
QTY 5: 4 x 4cm die with 125um thickness
QTY 5: 4 x 4cm die with 150um thickness
QTY 5: 8 x 8cm die with 200um thickness
QTY 5: 8 x 8cm die with 250um thickness
QTY 5: 8 x 8cm die with 300um thickness
Reference #225900 for specs and pricing.
Ultra-Thin Silicon die with Gold Metallization
A Process Development Engineer requested a quote for the following.
Description- The process above is requested in order to form Metallized silicon dies. Requested wafers- Ultra-Thin Silicon wafer (100/150/200mm diameter, 25±2.5um thick), polished and diced. Diced wafers will be delivered on tape with metal frame. Metallization stack- Au (minimum 300nm) + Seed layer for adhesion.
Metallization can be on both sides or single sided. Dimensions of diced dies- Width- 300±25um Length- 1000±25um Thickness- 25±2.5um
Reference #269568 for specs and quantity.
Researching Die Products and Polymeric Materials
A semiconductor material development researcher requested the following quote.
We are interested in some wafers for semiconductor media material development purposes. We are looking to recreate and research interactions between die products and our polymeric materials. Could you advise on which product IDs would be a good fit? 1) Silicon wafers - Previously we have used 4" wafers provided from a research facility which I assume would be similar to your silicon wafer product # 452.
I see this is currently out of stock with 5 week LT, would # 592 be a good substitute? What is your particle spec for Test Grade vs Prime grade? If we needed Prime grade, what is a good equivalent for # 452? 2) Gold coated Si wafers - We have also observed that gold-coated silicon die products are more sensitive to our materials and want to recreate this. The exact specs are proprietary to our customer (and unknown to us) but your typical deposition process should be sufficient for our purposes. Dicing - Can these both be diced to 11x7mm size? Quantity - Can I get the prices for 1x and 2x 4" wafers (both Si and gold-coated) diced to 11x7mm?
Reference #268821 for specs and pricing.
Silicon Dies Attached to Glass With Metal Patterning
An assistant professor requested the following quote.
Question:
For a research project, we'd like to process a silicon die (2mm x 2mm to 5mm x 5mm) where we thin the substrate to 50um and attach glass to the backside with some metal patterning on the glass (resolution of the order of 20um). Is that some that university wafer can do? The quantity would be around 20 die. If so, I'd be grateful if we could have a brief discussion regarding methodology and limitations.
Answer:
- We will coat a 1" glass substrate with certain metal for example, Al, Ti/Au, or Cr/Au, or other metals the client wants.
- We will bond a 1" 50um Si with this glass substrate using our polymer bonding agent.
- Then we die the composite wafer into dies, clean, and sort them into Gel box for final shipment.
Reference #148749 for specs and pricing.
Silicon Dies for Destructive Testing
A PhD candidate researching discrete power devices requested a quote for the following.
We are working on a new die-attach technology, and I’d like to get some 725um silicon die for destructive testing (thermal shock, adhesion, etc) on the lamination between the die and an aluminum heat spreader.
The requirements are pretty bare-bones:
- Silicon is required, but I don’t care about quality.
- The topside needs to be electrically conductive (by whatever means) and the bulk of the material needs to be an insulating, as we want to monitor the lamination’s capacitance with environmental stress (delam shows up in non-destructive capacitance tests).
- To maximize laminar stress, I’d like the die to be fairly large (am checking on what might best), but I do have flexibility depending on availability, cost, etc.
Reference #193629 for specs and pricing.
Silicon Test Die Used for Adhesive Testing
A postdoc requested a quote for the following:
Looking for test die:
- 1000 micron x 1000 micron square x 500 micron thick.
- 2000 micron x 2000 micron square x 500 micron thick.
Quote for Quantities of:
200, 1000, and 10,000
This is for adhesive testing. We are most interested in consistent backside.
We are setting up a test to measure die shear adhesion in accordance with “MIL STD-883E Method 2019.5 Die shear Strength”. We manufacture adhesives and we want to determine how well our materials adhere silicon die to various substrates.
We need consistent die size and consistent backside surface so we will achieve reproducible results. We haven’t settled on a standard size yet, so we want to look at both the 1 mm, and the 2 mm square die, and see which works best for us. So we would like to buy a small quantity of each size first, do some testing and then we would buy a larger amount for ongoing tests.
To summarize, we need silicon die with consistent surfaces, and consistent size. Electrical properties are not important. I requested a thickness of 500 microns, but as long as our tool can grab the die and shear it, the test should work. So other thickness might also work. What are your best prices for these requirements?
Answer:
If your adhesive can be used in vacuum at up to 500ºC, then we would be happy to use it ourselves.
For your application, we can supply you a single 100mmØ×500µm Silicon wafer and dice it into either 1,000×1,000µm or 2,000×2,000µm squares. A single 4"Ø wafer will yield at least 2,200 of 1mm squares or 780 squares, or we can even make it into 1,000 of 1mm squares plus 400 of 2mm squares. The diced squares would be shipped adhering to dicing tape, and the whole array packed in a single-wafer container. The individual squares can be picked off the dicing tape with tweezers or a vacuum wand. We can even send the dies on an "expander tape" if that will help you.
For the 4"Ø wafer surface and so the surfaces of the dies, you should consider a polished surface and an alkaline etched surface. We can even make the wafer with one side polished and the other side alkaline etched. The dicing tape can adhere to either the polished or the alkaline etched side (the dicing saw would cut from the opposite side).
The polished side, produced by the CMP process has surface roughness of about 1nm; it looks shiny black and is extremely reflective. Alkaline etched surface is composed of a multitude of pyramid shapes {either square base or triangular base - depending on crystal orientation of the wafer surface}. The pyramids are 1 to 10µm in height and they look matte silver.
For us to quote a price, you need to specify the following:
1. Do you want the wafers Alkaline etched, or One-side-polished (the other Alkaline etched) or Both sides polished ? Do you want wafer surface to be (100) or (111) orientation ?
2. Is the suggested method of packing suitable for you? Do you want to use expander tape?
3. How many squares of each size do you want?
Question:
500 °C is quite high. Do you have a material you are using now that withstands 500C, or is this a new requirement?
I had a few questions on the information you sent:
I read that 100 orientation has fewer bonding sites on surface. Would you expect the surface to be more consistent over time then?
What is the function of the expander tape? Does it create a gap between the die and so makes it easier to pick up with tweezers?
Is there any residue left on the die from the dicing tape? As long as it is typical of what a customer would see, it is probably fine. If not then we would probably want to have the side we are going to test away from the dicing tape.
I like the idea of having different surfaces on the top and bottom of the die. Is there a large increase in price for this?
Answer:
YES, it is a new requirement. So far we use microcrystalline waxes, some of which soften at rather high temperature, but we would like to go higher.
- I do not know what orientation surface would be more stable over time. I think that they are all very stable. Certainly (100) orientation is used more often, it has 4 directional symmetry constant with square shapes.
I expect that you want to dice (100) surface along (011) cleavage planes, that is parallel and perpendicular to the wafer Primary Flat.
- Yes, expander tape stretches to create bigger separation between dies.
- Dicing tape leaves no measurable residue. It is universally used to dice wafers.
- The cost is the cost of the wafer, the cost of the packing and the dicing cost which is proportional to the total length of the cuts. A major cost is the cost of setting up to do just one wafer. To do two or more dice sizes on one wafer is not a significant cost.
Question:
We would like a quote as follows:
- One 100 mm wafer diced into 1000 x 1 mm square die, plus 400 x 2 mm square die. Total 1400 die.
- Expandable tape
- One surface alkaline etched, the other surface polished
- Dicing tape adhered to alkaline etched surface
- Wafer surface 100 orientation, diced along 011 cleavage planes
Our adhesives are epoxy based, and will typically start to see some decomposition at around 300 °C. They are thermosets, and so do not melt. I am curious though, about your application. Are you adhering die to a substrate with this adhesive?
Here are the specs that we quote:
Item Qty. Description
EZ24b. 1 Silicon wafers, per SEMI Prime, P/E 4"Ø×525±25µm,
p-type Si:B[100]±0.5°, Ro=(1-20)Ohmcm, TTV<10µm, Bow<40µm, Warp<50µm,
One-side-polished, Back-side etched SEMI Flats (two),
Diced into at least 2,200 of 1,000×1,000µm squares,
Packed adhering to dicing tape, sealed in single-wafer container.
Reference #224824 for specs and pricing.
What is a Silicon Die?
A silicon die is a small, flat piece of silicon that contains a circuit, typically a microchip or integrated circuit (IC). It's the fundamental building block of modern electronic devices. Here's a breakdown of its key aspects:
-
Manufacturing Process:
- The die is created from a larger silicon wafer, which is a thin slice of silicon crystal. During
manufacturing, multiple identical circuits are etched onto the wafer using photolithography and other semiconductor fabrication processes.
- After the circuits are created, the wafer is cut into individual dies, each containing one of these circuits.
-
Function:
- The silicon die forms the core of many electronic devices, such as microprocessors, memory chips, and other ICs. It is where the actual electronic components, like transistors, capacitors, and resistors, are integrated.
- These components are interconnected to perform specific functions, such as processing data, storing information, or controlling electrical signals.
-
Packaging:
- Once the die is cut from the wafer, it is typically encased in a protective package with metal pins or solder balls that connect the die to the outside world. This package allows the die to be mounted on a printed circuit board (PCB) and integrated into electronic systems.
-
Applications:
- Silicon dies are used in virtually all modern electronic devices, including computers, smartphones, cars, medical devices, and more.
In summary, a silicon die is the core of an integrated circuit, responsible for the essential functions of electronic devices.