Ion Implantation and Silicon Wafers
A doctoral student asked the following question:
We have ordered the 3-inch Si wafer from University Wafer, and the item ID is 978. As we know, this wafer is B-doped Si wafer with 1-10 ohm cm resistivity. Can I know what doping method is used for this wafer?
I wondered what method is used for boron doping like ion implantation?
UniversityWafer, Inc. Quoted:
An open diffusion method of doping a silicon body with boron. In a first open diffusion heating step, a boron glass is deposited upon the silicon body with a silicon-rich boron phase (SiB 6) formed beneath the glass where deposition is directly on silicon.
Ion implantation is another way to doping while the Silicon wafers were polished finished.
Reference #272349 for specs/pricing.
The silicon wafer is used for several different applications. The most common use is to build computer chips. The silicon that is used must be processed in a process that ensures that the silicon will not be damaged when placed into electronic devices. If a device needs to be used in a sensitive manner, the silicon must be processed to be as indestructible as possible. The process of ionization keeps this possible.
Get Your Quote FAST! Or, Buy Online and Start Researchign Today!
What Substrates are Typically Used in Ion Implantation?
Ion implantation is typically used on substrates that are commonly used in the semiconductor industry, such as silicon, gallium arsenide, and indium phosphide. These materials are chosen because they have desirable electronic properties, making them suitable for use in the manufacture of microelectronic devices.
Silicon is the most commonly used substrate for ion implantation because it is abundant, has good thermal and electrical conductivity, and can be easily processed into wafers.
are also used as substrates for ion implantation because they have higher electron mobility and faster switching speeds than silicon, making them suitable for high-performance devices.
In addition to these materials, other substrates can be used for ion implantation depending on the specific application. For example, diamond and graphene are being investigated for their potential use as substrates for ion implantation due to their unique properties, such as high thermal conductivity and mechanical strength.
What is Silicon Ion?
Silicon ion refers to an ion that is formed from the element silicon by losing or gaining electrons. Silicon is a chemical element with the symbol Si and atomic number 14. It is a metalloid that is widely used in the electronics industry to make semiconductors, which are essential components in electronic devices such as computers and smartphones.
When a silicon atom loses or gains electrons, it becomes an ion. A silicon ion can have a positive charge if it loses electrons, or a negative charge if it gains electrons. For example, a silicon ion with a positive charge, written as Si+, has lost one electron, while a silicon ion with a negative charge, written as Si-, has gained one electron. Silicon ions can be found in various compounds, such as silicon dioxide (SiO2), which is commonly known as silica or quartz.
What is Ion Implantation?
Ion implantation is a process used in the semiconductor industry to introduce dopants or impurities into a material, typically a silicon wafer, in order to alter its electrical properties. This process involves the acceleration of ions, such as boron or phosphorus, to high energies and then directing them towards the surface of the material to be implanted.
During the process of ion implantation, the high-energy ions penetrate the surface of the material and become embedded in the crystal lattice of the material. This alters the number of electrons in the lattice and can create either a p-type or n-type semiconductor. The doping process helps to create regions of differing electrical conductivity, which are necessary for creating the structures needed in microelectronic devices such as transistors and diodes.
Ion implantation is a critical step in the manufacturing of semiconductors and is used to create precise doping profiles for the production of integrated circuits. The process is also used in other industries, such as the aerospace industry, to modify the surface properties of materials.
Silicon Wafers Ion Implantation
An assistant professor requested a quote for the following project:
I am planning to make a MOSFET device. So, I wondered do you have the Si wafer that has been ion implantation treated. It seems like this. Part of the wafer is N type but the most of the wafer is P type. Or do you have special wafer design quote service?
Reference #265599 for specs and pricing.
Boron Ion Implantation with Different Doping Concentrations
A Sr. Process Development Engineer requested the following quote:
We are very interested in purchasing doped polysilicon wafers (4-inch or 6-inch wafers). What kind of any polysilicon wafers that your company have? And also, may we know about any other specifications that you will need to know about our request? We look forward to receiving your information. The doping concentration (Boron) might be 1 x 10^20/cm^-3.
We are very interested in purchasing doped polysilicon wafers (4-inch wafers) with the following specifications.
Silicon Dioxide (SiO2) thickness = 1 um
Polysilicon thickness = 120 nm
Doping concentration
20 wafers
Are you able to process the Boron ion implantation with the different doping concentrations into the polysilicon layer (i.e. a certain doping concentration for every two wafers)?
The thickness of silicon dioxide (SiO2) is 1 micron. We also request for the double side polished wafers (DSP).
Based on your emails, you provide us only the polysilicon wafers (4-inch wafers) without any doping layer. Am I right?
May we know about any specifications regarding the polysilicon processing parameters, please?
UniversityWafer, Inc. Quoted:
Diameter 100mm SSP
Silicon Dioxide (SiO2) thickness = 1 um
Polysilicon thickness = 120 nm
Reference #265787 for more specs and pricing.
Can Ultrathin Freestanding Silicon Wafers Withstand Ion Implantation?
A postdoctoral fellow of a large University electrical & computer engineering department requested the following:
We are very interested in your ultrathin silicon wafers (we are looking for 5-10um thick freestanding Si wafers that are double side polished). However, since we have never used ultrathin wafers before, we have additional questions: Can the ultrathin silicon wafers withstand fabrication processes, such as ion implantation, sputtering, evaporation, bonding to other wafers, etc. Essentially, we want to perform ion implantation on one side, evaporate or sputter a metal on this side, and then bond this same side to a handle wafer. Then, on the other side, we want to grow various materials and conduct lithography. Do you see any of this being an issue when using the freestanding, ultrathin Si wafers?
UniversityWafer, Inc. Answered:
Ultrathin silicon wafers can withstand many of the standard fabrication processes, such as ion implantation, sputtering, evaporation, bonding to other wafers, etc. However, the thickness of the wafer must be taken into account when designing the fabrication process, as the thinness of the wafer can make it more susceptible to damage or warping during processing.
For example, ion implantation may cause damage to the crystal lattice structure of the wafer, which can result in defects or cracks. This can be mitigated by adjusting the ion energy and dose, as well as using specialized annealing processes to repair any damage.
Sputtering and evaporation processes can also be adapted for ultrathin wafers by adjusting the deposition rates and temperatures to prevent warping or cracking. Similarly, bonding techniques can be optimized to minimize stress on the wafer during bonding to prevent damage.
Overall, ultrathin silicon wafers can be used in many standard fabrication processes, but specialized process optimizations may be required to ensure successful manufacturing.
Reference #267507 for more specs and pricing.
What is the Imortance of Silicon Wafers in The Ion Implantation Process?
The medical device industry is making strides forward in numerous areas, including the field of electronic devices. The latest advancement in this field is the use of silicon wafer fabrication with bipolar components to create conductive aligners for implanted electronic devices. This type of method has made it possible for the creation of high quality, flexible electronic devices for use in a variety of application areas. One such application area is the electroplating of prosthetic joints, which is the basis for the manufacture of prosthetic limbs and joints in dogs and cats. The animal models used in the studies of this new process showed that the new material created by this method enabled the device to adhere to the natural surface of the animal, allowing the implant to be easily integrated into the joint.
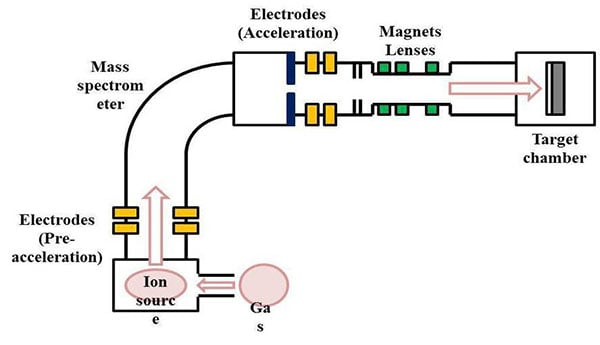
Silicon Ion
Another area in which the new material is finding application is the field of photonics and nanotechnology. With the use of silicon wafer fabrication, the ability to produce highly efficient, energy efficient and cost effective thin films is becoming widely available. The use of these types of emitters has helped to advance the capabilities of solar panels and other types of alternative power production systems. In fact, some of the better emitters now available can power a small home appliance, including hair dryers and air conditioners.
In general, the type of silicon wafer fabrication system that is used to produce these types of devices is called a bifocal lens. The lens is used to focus light in a focused manner, so that an extremely thin barrier forms around the receptive metal surface of the device. The thickness of this barrier will depend on the specific application and the specific device being fabricated.
When it comes to the process of ion implantation, the silicon wafer fabrication system produces devices that contain individual positive and negative ions. These individual ions are captured by an electrode that is present in the device. When the electrical current is applied to this electrode, the individual ions are knocking loose. The electrical current then causes the atom to break free from its neighboring atoms, thus creating a migration of the charged particles throughout the bulk of the silicon wafer fabrication structure.
As the charged particles move through the structure, they collide with neighboring atoms and become excited. This excited state is very similar to that which we feel when touching an electrified object, such as a pen or a finger. Because of this, the electric field associated with the atom is forced to push the negatively charged particle out of the bulk and towards an area of low electrical field.
Ion implantation in the process of silicon wafer fabrication allows light to be passed through the material. The light is captured by the silicon atoms and the atoms push the light through the structure. The light is trapped and pushed back into the cavities after it has passed through the structure. The light and the electric field created by the implantation process is what allows light to pass through and create images on the surface of the silicon wafer.
Silicon in the design of a computer chip or other electronic device must be shielded from impurities. The process of implantation allows the silicon to be both inside and outside the device. This allows the device to be able to function without worry about being damaged by the impurities of silicon, which can include traces of graphite or metal flakes that can interfere with the operation of the chips. The process of ion implantation also allows the user to have a more aesthetically pleasing device because the light that is trapped will allow the user to see the wafer as a whole, rather than being trapped by a grain of silicon.
The silicon wafer is used for several different applications. The most common use is to build computer chips. The silicon that is used must be processed in a process that ensures that the silicon will not be damaged when placed into electronic devices. If a device needs to be used in a sensitive manner, the silicon must be processed to be as indestructible as possible. The process of ionization keeps this possible.
The medical device industry is making strides forward in numerous areas, including the field of electronic devices. The latest advancement in this field is the use of silicon wafer fabrication with bipolar components to create conductive aligners for implanted electronic devices. This type of method has made it possible for the creation of high quality, flexible electronic devices for use in a variety of application areas. One such application area is the electroplating of prosthetic joints, which is the basis for the manufacture of prosthetic limbs and joints in dogs and cats. The animal models used in the studies of this new process showed that the new material created by this method enabled the device to adhere to the natural surface of the animal, allowing the implant to be easily integrated into the joint.
The medical device industry is making strides forward in numerous areas, including the field of electronic devices. The latest advancement in this field is the use of silicon wafer fabrication with bipolar components to create conductive aligners for implanted electronic devices. This type of method has made it possible for the creation of high quality, flexible electronic devices for use in a variety of application areas. One such application area is the electroplating of prosthetic joints, which is the basis for the manufacture of prosthetic limbs and joints in dogs and cats. The animal models used in the studies of this new process showed that the new material created by this method enabled the device to adhere to the natural surface of the animal, allowing the implant to be easily integrated into the joint.
Another area in which the new material is finding application is the field of photonics and nanotechnology. With the use of silicon wafer fabrication, the ability to produce highly efficient, energy efficient and cost effective thin films is becoming widely available. The use of these types of emitters has helped to advance the capabilities of solar panels and other types of alternative power production systems. In fact, some of the better emitters now available can power a small home appliance, including hair dryers and air conditioners.
In general, the type of silicon wafer fabrication system that is used to produce these types of devices is called a bifocal lens. The lens is used to focus light in a focused manner, so that an extremely thin barrier forms around the receptive metal surface of the device. The thickness of this barrier will depend on the specific application and the specific device being fabricated.
When it comes to the process of ion implantation, the silicon wafer fabrication system produces devices that contain individual positive and negative ions. These individual ions are captured by an electrode that is present in the device. When the electrical current is applied to this electrode, the individual ions are knocking loose. The electrical current then causes the atom to break free from its neighboring atoms, thus creating a migration of the charged particles throughout the bulk of the silicon wafer fabrication structure.
As the charged particles move through the structure, they collide with neighboring atoms and become excited. This excited state is very similar to that which we feel when touching an electrified object, such as a pen or a finger. Because of this, the electric field associated with the atom is forced to push the negatively charged particle out of the bulk and towards an area of low electrical field.
Ion implantation in the process of silicon wafer fabrication allows light to be passed through the material. The light is captured by the silicon atoms and the atoms push the light through the structure. The light is trapped and pushed back into the cavities after it has passed through the structure. The light and the electric field created by the implantation process is what allows light to pass through and create images on the surface of the silicon wafer.
Silicon in the design of a computer chip or other electronic device must be shielded from impurities. The process of implantation allows the silicon to be both inside and outside the device. This allows the device to be able to function without worry about being damaged by the impurities of silicon, which can include traces of graphite or metal flakes that can interfere with the operation of the chips. The process of ion implantation also allows the user to have a more aesthetically pleasing device because the light that is trapped will allow the user to see the wafer as a whole, rather than being trapped by a grain of silicon.
The silicon wafer is used for several different applications. The most common use is to build computer chips. The silicon that is used must be processed in a process that ensures that the silicon will not be damaged when placed into electronic devices. If a device needs to be used in a sensitive manner, the silicon must be processed to be as indestructible as possible. The process of ionization keeps this possible.