Substrates Used For Pulsed Laser Deposition (PLD)
A research scholar requested a quote for the following.
Could you please let me know the price of the semiconductor pallets that used as a target material in pulsed laser deposition technique.
need GaN, CdTe and TiO2 traget materials, one
piece each. The diameter should be 1.5 cm and thickness 0.2/0.3 cm.
Purity level should be 99+. If possible please send me the price and
specification of all these materials.
UniversityWafer, Inc. Answer:
We can supply appropriate semiconductor target materials, Silicon, Germanium, III-V semiconductors etc. You need to specify which material you need, its purity level and the dimensions of you target and if its surfaces need to be polished.
Also, do specify how many you need.
Reference #109573 for specs and pricing.
Get Your PLD Quote FAST! Or, Buy Online and Start Researching Today!
Gallium Phosphide (GaP) Wafers for Pulsed Laser Deposition (PLD)
A Phd candidate requested a quote for the following:
I would like to use a thick GaP wafer as substrate of a thin film. The diameter of the substrate should be 30mm and the thickness 3mm. The orientation of the GaP crystal is of minor importance. I'm not sure if the resistivity has an influence on the THz radiation transmission? In any case it should as transparent as possible for THz radiation. Also it would be important that the parallelism of the back- and front-surface is as good as possible. Do you in general consider to fabricate custom products and can you estimate the price of my custom wafer?
My setup is working in the range from 0.1-3THz, which corresponds to a wavelength range of 3000-100um. The GaP wafer should therefore be transperent in this light spectrum. But since we use also other setups it would be better if the wafer would be transparent up to 8THz.
Since I'm using the GaP as substrate for a vanadium dioxide thin film and especially since I plan to do ellipsometry measurements I need a pure substrate without anti reflection coatings. Otherwise I would have refections coming from these layers.
We need both sides to be polished.
The number of wafers that we would order depends a bit on the price. At the moment we would order at least three of them.
I know that GaP has a cubic lattice structure. What's the difference then between different GaP orientations?
This GaP wafer should survive a temperature of 500-600°C without any change in structure and shape, right? Because for the Pulsed Laser Deposition (DLP) of vanadium dioxide we would need to heat the GaP up to this temperature.
Is there a global shortage in undoped GaP? Another company told me that they don't have any GaP crystals at all at the moment.
UniversityWafer, Inc. Answered:
We have some 25.4mmØ GaP crystals from which we can readily produce 3 to 5 wafers, 3mm thick.
Their parameters are:
1. "As-Cut" 25.4mmØ×4mm - n=1.6E15/cm³, u=120cm²/Vs, EPD=7E4/cm²;
2. "As-Cut" 25.4mmØ×?mm - n=3.4E15/cm³, u=140cm²/Vs, EPD=8E4/cm².
We have other (larger) GaP crystals but more heavily doped which may or may not be suitable, depending on the spectral band of interest.
Attached is a Transmission spectrum for GaP material similar to crystals 1. and 2. above, over the wavelength of 560 to 3,300µm and so covering the lower THz range.
Note that this is Transmission (in air), rather than Absorption, so it does not approach 100%. The difference between what is shown and 100% is due mostly to surface reflections caused by the high refractive index of GaP.
In the upper THz range which is the IR wavelength range (0.3-600)µm, the Transmission and Absorption spectra are much more complex. The material is opaque at 0.3µm, entirely transparent around 1µm and with multiple absorption bands between 3 and 600µm. Through out this interval, but especially around 1µm, Absorption is strongly affected by conductivity, hence Nc, hence the degree of doping.
As I wrote yesterday, do let me know what THz frequency range is of interest to you and I shall prepare quotes for GaP material suitable for you.
Wafers 25.4mmØ, would these be adequate, or must they be 30mmØ ?
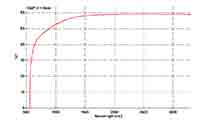
Reference #203618 for specs and pricing.
Thermal Oxide Coated Silicon for Pulsed Laser Depositon
We just need 1um thermal oxide (SiO2) on Si (001)wafer. I used this wafer just as substrate for my pulsed laser deposition. So I used wafer that is in our lab. So I did not know which kind of wafer is best for my study. Usually I try to etch it during 10sec using HF to remove oxide layer after cleaning. I think that one container is including of 25 wafers. Is it right? I want to order 1 container (minimum quantity) for this time.
The wafer’s quality (including of resistivity or some properties) is not matter for my study. I just need for (100) direction, one side polished, 4inch , 500~550um thickness and 1um oxide layer on wafer. Doping is also no matter. If intrinsic Si wafer is cheaper than P-Type or N-types, it is ok. This is first time to purchase wafer so I can’t easily decide best one because I have no information about Si wafer. Sorry about it. Could you suggest best one for my request? Also I have one question. Do you have fused silica wafer?
Could you send quotation for me?
UniversityWafer, Inc. Quoted:
Wet Thermal Oxide Wafer Sale 25 wafer minimum. We also have the following Silicon special we can put oxide or nitride on them:
100mm P/B (111) 40-60 ohm-cm 255um SSP Prime
Wet, Dry oxide and LPCVD NItride at Bottom - please scroll down.
100mm P/B (100) 1-10 ohm-cm SSP 500um
Wet Oxide
100nm-500nm
600nm-1,000nm
2um-3um
5um also available
100mm N/Ph (100) 1-10 ohm-cm SSP 500um Wet Oxide
100nm-500nm
600nm-1,000nm
2um-3um
5um also available
Stoichiometric LPCVD Nitride
100mm P/B (100) 1-10 ohm-cm SSP 500um
50nm-200nm
201nm-300nm
301nm-500nm
Stoichiometric LPCVD Nitride
100mm N/Ph (100) 1-10 ohm-cm SSP 500um
50nm-200nm
201nm-300nm
301nm-500nm
Low Stress and Super Low Stress Nitride Also Available
Reference #114676 for specs and pricing.
What Is Pulsed Laser Deposition (PLD)?
Pulsed Laser Deposition (PLD) is a versatile thin-film deposition technique used to create high-quality films of various materials. Here’s an overview of the process and its key aspects:
Process Overview
- Laser Pulse Generation: A high-power pulsed laser is focused onto a target
material placed inside a vacuum chamber.
- Target Ablation: The laser pulse hits the target, causing rapid heating and ablation of the material. This creates a plasma plume composed of the ablated material.
- Material Deposition: The ejected material from the plasma plume travels towards a substrate, where it condenses and forms a thin film.
- Film Growth: The film grows layer by layer on the substrate. The properties of the film can be controlled by adjusting various parameters such as laser energy, pulse duration, substrate temperature, and ambient gas pressure.
Key Aspects
- Material Versatility: PLD can be used to deposit a wide range of materials, including metals, semiconductors, oxides, and complex compounds.
- High Purity and Quality: The films produced by PLD are typically of high purity and can have excellent crystalline quality.
- Control Over Film Thickness: The thickness of the deposited film can be precisely controlled by adjusting the number of laser pulses.
- Complex Stoichiometry: PLD is particularly effective for depositing materials with complex stoichiometry, as the ablation process tends to preserve the target composition in the deposited film.
- Substrate Versatility: PLD can be performed on various substrates, including those with complex geometries.
Applications
- Semiconductor Devices: Used in the fabrication of semiconductor thin films for electronic and optoelectronic devices.
- Superconducting Films: PLD is commonly used to produce high-temperature superconducting films.
- Protective Coatings: Used to create durable and high-performance protective coatings for various industrial applications.
- Optical Coatings: Employed in the deposition of optical coatings for lenses, mirrors, and other optical components.
- Research and Development: Widely used in material science research for the development and study of new materials and thin-film technologies.
Advantages
- Precision: Allows for precise control over the film composition and thickness.
- Versatility: Can deposit a wide variety of materials and accommodate different substrate types.
- Scalability: Suitable for both small-scale research applications and large-scale industrial production.
Challenges
- Equipment Cost: The setup for PLD can be expensive due to the need for high-power lasers and vacuum systems.
- Uniformity: Achieving uniform film thickness over large areas can be challenging.
- Deposition Rate: The deposition rate in PLD is typically lower compared to some other deposition techniques.
Pulsed Laser Deposition is a powerful tool in thin-film technology, offering unique advantages for creating high-quality and complex material films.
Sapphire Used For Pulsed Laser Deposition
A scientist requested help for the following project.
In my laboratory I have an Nd:YAG laser (Continuum Surelite III) with wave length 266 nm as part of a pulsed laser deposition system.
I was suggested by my contact at NEOCERA, the vendor of the PLD system, to place several 2 sides polished single crystal sapphire wafer to energy of the laser beam.
On your website I found two wafers that could suit my needs. Before purchasing it, I have a few questions:
for the ID: 1251, what does C-M plane 0.2 Deg mean?
for the ID: 2561, what does C-Plane TTV: <25µm Bow: <25µm, Orientation Flat (OF): 30±1mm, Ra<2nm mean?
- What is the optical transmission profile? in particular at 266 nm, what is the optical transitivity?
- How to the optical properties (transmission/reflection/absorption) depend on the orientation?
- Do you have any idea about the damage threshold (in terms of J/cm2), a parameter typical of laser windows?
UniversityWafer, Answered:
The customer seems will use this for laser application, we think you can try our sapphire wafers.
C-M 0.2 Degree means the cut orientation is C plane off to M plane 0.2 degree.
TTV: Total thickness valiation.
Bow: the bending.
Flat: off side, cut on A orientation.
Ra: Roughness.
Reference #224562 for specs and pricing.
What Substrates Are Used For Pulsed Laser Deposition (PLD)
The choice of substrate for Pulsed Laser Deposition (PLD) depends on the specific material being deposited and the intended application. Some common substrates used in PLD include:
- Silicon (Si): Widely used in semiconductor and microelectronics applications due to its compatibility with many materials and its well-understood properties.
- Sapphire (Al2O3): Frequently used for high-temperature superconductors and optoelectronic devices because of its high thermal stability and excellent optical properties.
- Magnesium Oxide (MgO): Often chosen for high-temperature superconductor films and magnetic materials due to its excellent lattice match with many materials.
- Strontium Titanate (SrTiO2): Preferred for oxide thin films, such as ferroelectric and dielectric materials, due to its perovskite structure and high dielectric constant.
- Lanthanum Aluminate (LaAlO3): Another perovskite substrate used for complex oxide thin films, including ferroelectrics and high-temperature superconductors.
- Quartz (SiO2): Used for optical applications and as an insulating substrate in various electronic devices.
- Glass: Commonly used for applications where transparency and low cost are important, such as in display technologies and solar cells.
- Mica: Sometimes used for two-dimensional materials and thin-film studies due to its smooth surface and easy cleavage.
- Zinc Oxide (ZnO): Used for semiconductor applications, especially in optoelectronics and transparent conductive films.
The choice of substrate is critical for the quality and performance of the deposited thin film. Factors influencing this choice include lattice match, thermal expansion coefficient, surface smoothness, chemical compatibility, and the specific requirements of the intended application.